Digital Line of Sight
Will a Digital Twin Become a Key Element of Your Digitalization Strategy to Reduce Risk and Enable Operational Excellence?
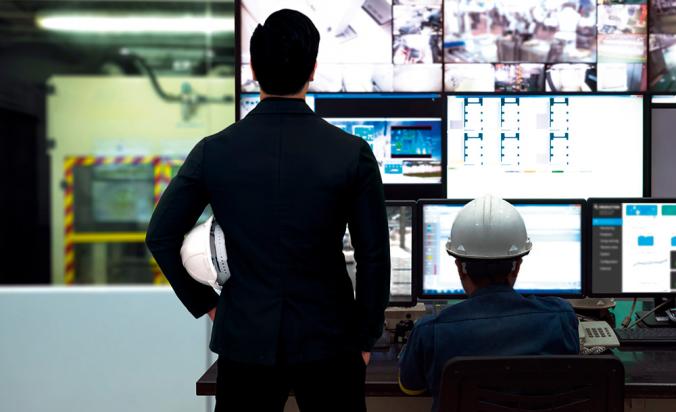
Digital line of sight is a digital connection (or thread) of data throughout an asset’s lifecycle to ensure information integrity, accuracy, and timeliness to access. There are many reasons for an organization to have a digital line of sight. However, not all of the reasons to implement digital line of sight are to realize the assets’ value, some organizations use digital line of sight to help ensure corporate reputation and positive public relations, as well as to ensure happy and safe workers.
Asset management standard ISO 55001 introduced a structured way in which to perform best-in-class asset management and suggests that there needs to be alignment from the corporate goals to the asset management policy to the asset management plans and tactics used on each asset under management. This alignment is the line of sight that enables individuals and teams to understand how their day-to-day actions match up with long-term corporate goals.
Putting a digital line of sight in place is essential when seeking to achieve business objectives and efficiently deploy scarce resources. This process is necessary for organizations to execute in order to excel in the future and deal with their younger workforce – digital natives who are inexperienced but expect access to information at their fingertips.
With the massive amount of data involved in managing assets, it is imperative that line of sight is digitally supported, ideally through an evergreen and immersive digital twin.
The Backbone of a Good Asset Management System
Connecting as-designed, as-built, and as-operated information to the digital twin in an open, connected data environment enables management to make fast and accurate decisions, and workers are more productive when they know the reasons behind their daily activities.
Digital line of sight connects the leaders of the organization, the assets they manage, and the workers to align work execution on business-critical assets to realize maximum value. The asset is the center of the universe in that it has been purchased to perform a function to create value to the organization. How an asset is managed depends on the current and future objectives of the organization and the risk it poses to the organization and the public if it fails to fulfill that function sufficiently. The workforce should only do the minimum amount of work to ensure that the asset functions to the necessary performance level to attain the objectives.
While value is the ultimate goal we want to attain from our assets, it is also the key measure of our performance. We also should create value for customers and the public while meeting the requirements and targets set by our regulators.
Digital line of sight can be achieved through a digital twin, that is, a digital representation of the physical asset and its associated processes and systems, including all the relevant information that allows you to understand and model its performance. Typically, a digital twin can be continuously synchronized from multiple sources, such as sensors and continuous surveying, to represent its nearly real-time status, working condition, or position. Digital twins are used to optimize the operation and maintenance of physical assets, systems, and manufacturing processes.
Plainly stated, a digital twin is a highly detailed digital model that is the counterpart (or twin) of a physical asset. Connected sensors on the physical asset collect data that can be mapped onto the digital model. Anyone looking at the digital twin can view crucial information about how the physical asset is performing in the real world so that the workers can easily see the relationships between data points and quickly make informed decisions to enable timely correction to poorly performing assets.
Line of sight should be two-way or bi-directional; corporate objectives flow down to the workers so they know where to focus and spend their asset management efforts and process adherence metrics flow up as key performance indicators (KPIs). Having a digital line of sight also enables conformity and assurance within your processes. The executives set corporate objectives and targets, and then asset management decisions can be made and policies can be put in place based on those goals.
KPIs are used to measure attainment to objectives, they show how the operation is performing, both for output and for adherence to process. In addition to KPIs, asset condition data also helps the workforce make decisions about which assets to focus on to ensure that business objectives are met. These decisions can be for minor repairs, refurbishment, or capital replacements. Once the “bad actor” assets are identified, the digital line of sight becomes even more important because it enables safe and efficient work to be performed to bring the assets back to good condition.
Access to design data and settings allow workers to make safe corrections to production upsets. This is especially effective when connected with the asset condition data and current operating context of the asset. Without digital access to the current asset configuration and the ability to compare to the design basis, disaster can be the result. Workers often need more access to the knowledge base, whether it is to prepare for a job or to understand a new asset or process being worked on. This knowledge base should include things like failure modes and effects analyses (FMEAs), which document the asset functions, the ways in which the asset can fail to function, the business impacts of these failures, and the prescribed mitigation tasks that should be executed to detect and correct asset functional failures. The knowledge base also includes manuals, P&IDs, drawings, workflows, procedures, and task instructions so that the job can be done safely and in a timely manner.
Without a digital line of sight, the work cannot be as easily done without wasting time looking for parts and instructions, knowing the settings and condition of the asset in question and those of adjacent or connected assets up and downstream. Lastly, as workers benefit from digital line of sight, so will the organization because objectives are met faster and more shareholder values are realized at a lower overall operation cost.
Examples
Here are some examples of digital line of sight for executives and for workers.
Workers with Digital Line of Sight
Workers access the digital twin to know where to focus their attention and manage by exception. They have access to all necessary data and documentation to execute the work safely and on time.
Management with Digital Line of Sight
Executives visualize the organizational and unit performance compared to the objectives and targets they have set.
Achieve operational excellence with minimum effort in the shortest time possible
Organizations will more easily attain their performance objectives and realize the best value from their assets if they enable digital line of sight. This will help the workforce reach high levels of operational excellence with minimum effort in the shortest time possible. Failure to do so will perpetuate the struggle and lower performance achievements. Rather than considering digital line of sight as unattainable or as a luxury, leadership needs to consider enabling a digital line of sight as mandatory to optimize performance.
Digital line of sight can help with:
- Safe work execution
- Efficient work execution and optimal wrench time
- Fewer operational delays and less downtime
- Reduced procurement, expediting costs
- Safe reaction to production upset and safe shutdown
- Higher levels of operational excellence reached with consistency
- Workers are more productive
- Workers know the reason they are doing the activities they do on a day-to-day basis
- Shortened decision-making time, increased accuracy, and effective decision-making
- Enhanced outage planning and execution
- Performance aligned to corporate strategy and organizational goals
- Optimal TOTEX spend to attain organizational goals
- Reduction in risk associated with capital assets