Competence and Skills in the Era of Industry 4.0
Digitalisation, Industry 4.0 and IoT transform the industrial landscape at a breath-taking pace. The technological development is rapid, but the successful application also requires human skills and capabilities. What are the most topical issues that should be included in the curriculum of newcomers and for those already in the profession?
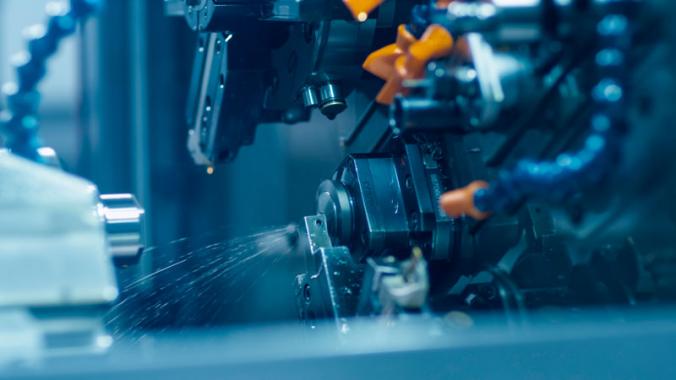
Digital transformation in the form of Internet of Things (IoT) or Industry 4.0 (I4.0) brings both challenges and opportunities to maintenance and asset management. The transformation makes available a broad variety of tools and technologies including smart devices and sensors, intelligent inspection, diagnosis and prognosis, cloud-based computing, simulation, location and tracking, and virtual and augmented reality (VR/AR) tools. Cloud technologies enable on-demand network access to shared information resources and mobile devices allow access to the necessary information from any location.
Simulation - combined with information collected from smart sensors, devices and information systems - enables virtual presentation of a physical system i.e. digital twins. Location and tracking technologies support operator and equipment identification and enable traceability of the past maintenance actions and geo-localisation.
Digital transformation influences maintenance, and asset management processes and offers solutions for more effective practices. The implementation of such technologies in current asset management practices is, however, not straightforward. Novel competencies and skills are needed when deploying and enrolling digital technologies into the operations and on different levels or organisation, and when maintaining intelligent equipment.
The training of both experienced employees and newcomers is necessary. What knowledge and skills do maintenance and asset managers need in their working life, and what skill and competence requirements does the rapid technological development impose? In this article, we highlight domains where special attention needs to be paid to the development of new skills and competences and the content of education at all levels.
Industry 4.0 induced competence needs
I4.0 and IoT are changing the industrial landscape requiring new capabilities for information management. Manufacturing companies are required to collect measured data, analyse it, refine information from it, and supplement the information from it with the knowledge of their employees. One success factor is flexibility, it is enabling production companies to produce and deliver products of high quality and to adapt quickly to customer requirements. When the data and the information is visible and available, companies can recognize things similar to each other and make quicker decisions.
Manufacturing companies want to become agile companies that react in real-time to occurring events and make data-based decisions [1]. Advanced information and communication technologies are growing in the industrial automation field and the Industry 4.0 is based on them.
While implementing Industry 4.0 successfully, the obtainable data should be prepared and processed in a way that it supports decision-making. The data may be useful if the technical requirements for real-time access are met and if there is an infrastructure with the necessary data processing and seamless data transmission.
Another principle for successful Industry 4.0 implementation is that manufacturing companies need IT integration to improve data use and increase agility [1]. IoT cloud computing architecture has a big role in IoT data management. IoT data and applications are stored in the cloud for easy access in any client software web browser.
The cloud computing architecture suits Industry 4.0 because of its centralized control accessibility for various users like managers, customers, operators, and programmers [2]. The collected data should be used to understand how the existing plants are running, to identify the inefficiencies in production capacity.
Cognitive capabilities are needed to convert the exploding big data to meaningful insights that further improve manufacturing processes and functions. In order to translate the patterns, anomalies and trends to predictions of remaining lifetime or future behaviour of an item, thorough understanding of the asset system is required. Traditional physical models are highly complicated and require a lot of modelling efforts to capture relevant behaviour.
Data-driven models and algorithms usually use pattern recognition and machine learning techniques to detect changes in system states. Qualitative information like risk and reliability analyses provide essential information about the target application. These analyses could provide cause-consequence chains that connect failure indication or initiation pattern or a deviation from a certain chain of events and link the emerging event with expected consequences.
This allows the user to make predictions and to take proactive actions in time. A further step to add value is to connect the data with business-related information like KPIs, life-cycle cost and profit model, or decision-making situation.
Despite the fast digital development, it is the responsibility of humans to interpret the outcomes of smart devices and systems. In smart maintenance, smart systems support the technicians and managers, but do not replace them. However, the employees working in the field often lack necessary technological competence and skills, and a large proportion of fieldworkers are unaccustomed to the use of digital technologies.
The employees feel that they lack analytical skills and the capability to interpret the data provided by novel sensors [3]. The technology has evolved so rapidly that relevant standards (e.g. EN15628:2014) do not take into account the existence or use of these technologies when defining the competence areas for a maintenance manager.
However, these competence areas can be extended to also cover the knowledge and skills that arise I4.0 [4]. As a conclusion, the maintenance managers are expected to use their technical/engineering knowledge and digital organizational tools to improve maintenance tasks and plan efficiency in terms of availability and reliability.
What skills do the engineers and technicians in the maintenance domain require in the future?
It has traditionally been thought that the competence profile of people performing maintenance activities includes, for example, maintenance and reliability engineering, standards, maintenance management skills and skills necessary for operating maintenance information systems. In addition, the understanding of the financial issues, contracting and health and safety assurance is regarded as necessary. Digitalisation, IoT and many other technological advancements, increasing value of data in decision making, networking and transformation towards holistic approaches as asset management pose novel competence requirements.
It is also evident that maintenance is not an isolated function in the company, but a business area that cooperates, and is coordinated with several internal and external partners. Maintenance personnel are expected to use their traditional skills and apply an increasing number of digital tools in an increasingly complex business and operational environment. This also requires interpersonal and interaction skills.
The required competencies and skills in the era of Industry 4.0 go beyond those defined e.g. in the standard EN15628:2014. An extended curriculum for educational programs as well as for continuing professional education and training is therefore proposed, with following topical content:
Maintenance professionals need the traditional core competence and knowledge on technical and engineering topics, and in addition, the skills to make use of modern digital technologies and tools to improve maintenance tasks and plan efficiency in terms of availability and reliability. In this domain, there is a need for continuing education and training for those already in the profession.
Asset management emphasises management skills, economic assessment methods and asset life cycle thinking. Education should go beyond the worldwide initiative CDIO and also incorporate economics, sustainability, and circular economy.
Data collection, analysis and refining calls for cognitive capabilities and competence to apply commercial tools in the prevailing operational and business environment, such as analytic reasoning and problem solving.
Networking, outsourcing and partnering requires not only capabilities in formulation of common goals, KPIs and contracts but good communication, cooperation and interaction skills. The experienced professionals would also benefit from continuing education.
Increasingly complex systems call for system thinking, and the ability to build up a holistic view of the positive impacts and negative consequences of decisions. This is tightly connected with engineering ethics.
Mirka Kans, Helena Kortelainen and Lasse Metso