Intelligent Leak Handling with the LeakExpert app
Do you really want to save your company money? Then eliminating compressed air leaks would be an important step forward.
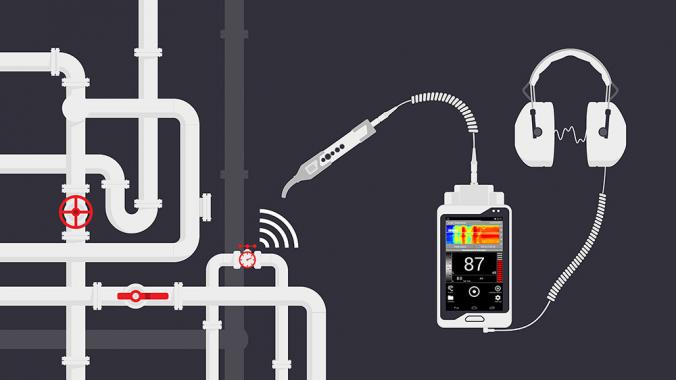
Text and photos: Sonotec
Compressed air is one of the most expensive energy sources and is responsible for 10% of industrial energy costs. 30% of this expensive energy is lost simply due to leaks in compressed air systems. This makes detecting and eliminating leaks worthwhile.
A digital ultrasonic testing device from SONOTEC makes it possible to detect leaks on compressed air and gas systems and on gas lines with pinpoint accuracy. Thanks to a new, intuitive app, leaks can also be evaluated automatically with the ultrasonic testing device. Additionally, the LeakExpert app makes it easier to generate a report as a decision-making tool for follow-up actions and as evidence of successful energy management in accordance with EN ISO 50001. This means that SONOTEC measuring technology helps pave the way for Maintenance 4.0.
Do you really want to save your company money? Then eliminating compressed air leaks would be an important step forward. The SONAPHONE ultrasonic testing device with the LeakExpert app for locating and evaluating leaks on compressed air and vacuum systems and gas lines a device that can help with the process. It can be operated intuitively and includes numerous innovative functions for search, evaluation and documentation. This is how it works:
The search for a leak begins
Switch on SONAPHONE with LeakExpert app, put on the headphones, and start the search. Here too everything depends on the right method and equipment. First insert the large acoustic horn on the device’s airborne sound sensor. Through this horn, the SONAPHONE receives noises in the ultrasonic range caused by the escaping of compressed air or the sucking in of ambient air into vacuum systems, and then transforms them into audible or visible signals. In this way the leak can already be heard from a distance of approximately eight meters. As soon as you receive a signal through the headphones, orient the ultrasound sensor toward the noise and switch the integrated laser pointer on. This will already allow you to roughly locate the leak. The closer you get to the leak, the clearer the ultrasound signal will become.
In the immediate vicinity of the leak, immediately switch from the acoustic horn to the precise locator. Then check the lines and connections in the previously located area until you have precisely identified the damaged area.
Evaluating the leak
To correctly evaluate the leak, you only have to enter your system pressure and the type of gas in the device and start the specially developed leak evaluation. With just a touch of a button, the measurement and evaluation of the leak will begin, whereupon the loss in liters per minute will be displayed to you immediately. Additionally, the device will rank the leak in a class from 1 to 5 (1 = small leak, minor loss [green]; 5 = large leak, very high loss [red]). This evaluation process is based on a procedure patented by Sonotec.
Documentation for management
The LeakExpert app offers the option of structured and process-supporting documentation. This is easier than it sounds, since the app guides you through the testing process step by step. First you identify the exact location of the leak by entering the building, area, system and component. This information is saved in the app and is available to you again for the next search. However, the LeakExpert app not only allows you to specify the location and size of the leak, but also to note if and how urgently the leak needs to be repaired and how extensive the expected repair efforts will be. Even the repair dates can be entered directly for each leak.
Next, photograph the area of the leak, flag the damaged area with a marker in the photo and save the image in a folder. You can also record a voice memo with special details about the leak that has been found and save this memo. Finally, you can mark the leak to be repaired with our LeakTag and then move on to the next leak.
After the testing procedure, with just a few clicks export a CSV or ZIP file into your maintenance system for further processing of the measurement data, or generate a PDF report. You can then compile the report itself individually depending on the requirements, and, for example, sort the leaks according to size.
All information on the leaks is saved in the device and can be called up again during the repairs. After the leak has been eliminated, the repaired location can be checked again with SONAPHONE and touched up if necessary. The successful repair is then also documented in the report – as evidence for management.
Conclusion
With the new SONAPHONE and the LeakExpert app, leaks on compressed air and vacuum systems and gas lines can be detected and evaluated with pinpoint accuracy. The multifunctional device with touchscreen processes the ultrasound signals directly. A report can be generated quickly and easily and used as a decision-making tool for follow-up actions and as proof of successful energy management. With a single click, the documentation of the results is available for management, with comprehensive information about the precise location of the leak, the energy loss, a photographic record and the priority level of the repair.
Additionally, by systematizing the search for leaks and their evaluation, the device contributes to significant time and cost savings in maintenance. Error-prone paper records are a thing of the past, since all data can be evaluated and updated directly in the device. This also facilitates the verification of energy saving measures in the context of the documentation obligation for companies that are certified in accordance with EN ISO 50001. The new device technology also helps to realize a verifiable energy savings of 5% so companies can retain their certificate and uphold their claim to a reduction of their Renewable Energies Act (EEG) cost apportionment and of their electricity and energy taxes.
Thus ultrasonic testing device not only is appropriate for leak detection and classification, but is also useful for tightness testing of unpressurized systems and condition monitoring through checking bearings. The new device is also used for electrical inspection by detecting partial discharges and for checking valves and steam traps.
sonotec.eu/products/preventive-maintenance/ultrasonic-testing-devices/sonaphone/