Connected Field Service
For many organizations, their history with maintenance operations and facilities management evokes a typical multi-system, break-fix reactionary model. In most cases, these applications would involve multiple disparate systems; one for controls, one for HVAC, one for security, one for work order management… Typically, few of these systems, often sourced from different vendors, would connect to each other or interact. Maintenance operations would wait until a problem occurred and then send a technician out with a work order.
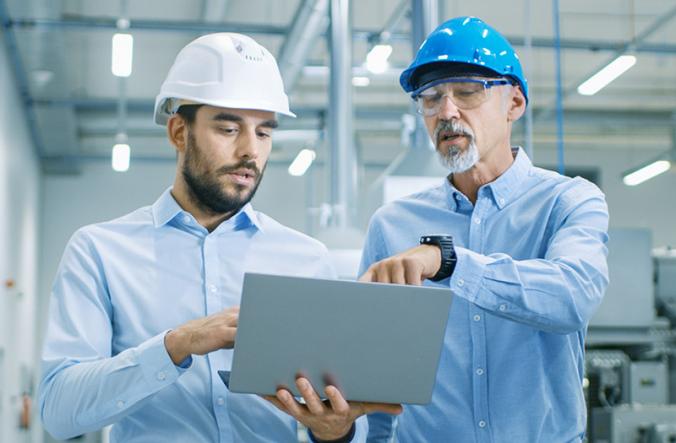
Often, that work order wouldn’t be overly detailed, might lack an equipment repair history, and provide little accompanying information past an equipment identifier and location. Of course, usually that work order needed to be completed quickly to free up that same technician for the next break-fix work order in the queue, never leaving time for the insightful correlation of underlying causes to possible maintenance-requiring symptoms.
Fortunately, technology within the facilities management industry has certainly progressed past a single break-fix option. Multiple technologies have emerged, then evolved, to make maintenance less reactionary and more proactive. Some of these technologies include the Industrial Internet of Things (IIoT), rapidly improving connectivity between networks, sensors, machines, and building system equipment. Next is the proliferation of mobile computing devices and, more specifically, devices that provide a head-mounted display combined with hands-free operation (e.g., Microsoft’s HoloLens holographic computer or RealWear’s HMT-1 head mounted wearable device). The additional integral ingredient to enable a cutting-edge Connected Field Service (CFS) solution is the software to tie it all together.
ICONICS, a global automation software vendor and six-time Microsoft Partner of the Year award winner, created its Fault Detection and Diagnostics-based Facility AnalytiX® software to provide maintenance personnel with a complete, ongoing commissioning solution to significantly reduce costs and improve operational efficiency. Facility AnalytiX incorporates user customizable fault rules to report faults; weighing the probability of equipment failures and advising personnel of immediate preventative actions that can be taken to reduce downtime, improve safety, and optimize energy savings.
Building upon the strength of its working relationship with Microsoft, ICONICS is now focusing its attention on the mobile aspect of Connected Field Services. The goal was to build a solution that not only lets users know when connected equipment uses too much energy or is about to fail (e.g., Fault Detection), but also delivers guaranteed notifications to the right service technician at the right time, with the correct required information, tools, and parts required to quickly resolve the issue. The heart of this solution, known as ICONICS CFSWorX™, packages those capabilities up into a convenient mobile app for today’s popular smartphones and mobile devices.
Microsoft has made significant investments in its Azure and Dynamics 365 platforms, enabling ICONICS to deliver a more powerful, integrated Connected Field Service solution than ever before possible. Those investments include Microsoft’s Azure IoT services, which allow users to “securely connect, monitor, and manage billions of devices to develop Internet of Things (IoT) applications”, and Microsoft Dynamics 365 for Field Service, which provides “built-in intelligence” to help “resolve service issues before they occur, reduce operational costs, and deliver positive onsite experiences.”
Customers are certainly seeing the benefit of this combination of IIoT, predictive analysis, and field service software. A typical maintenance scenario prior to these combined abilities would be as follows. A piece of equipment would generate an alert, such as an alarm or fault; perhaps that it was using too much power. A standalone process or building maintenance system would recognize the condition and send an alert. A maintenance manager would receive that alert and call a field technician to investigate the problem. That field technician may or may not be available to address the problem right away, potentially resulting in costly downtime and wasted energy. All in all, a very reactionary process.
Combining the power of ICONICS CFSWorX with Microsoft Dynamics 365 for Field Service and Azure IoT services changes this scenario. When the equipment generates an alert, CFSWorX uses a customizable weighted scoring system that factors in each technician’s schedule (on/off duty), availability (signal strength, battery life, device health), location (proximity to the issue), and skill level to determine which technician is best for the task and sends a notification to his or her mobile device. That technician can then accept, snooze, or decline the assignment through the CFSWorX app. If the issue is declined, the algorithm kicks back in and delivers a notification to the next best technician, and all actions are logged in a comprehensive audit trail for reporting, accountability, and training purposes. Upon arriving at the equipment in question, the technician is provided with full information on the problem at hand, along with a complete repair history and guidance towards required parts and tools. This is achieved by combining real-time information from ICONICS software with work order history and related information from Dynamics 365 in a unified interface, enabling the technician to make a fast, informed fix.
Increasingly, maintenance personnel are provided with state-of-the-art hardware technology to ensure correct repair procedures and save time and costs per service ticket. At the SPS IPC Drives event in Nuremburg, Germany, ICONICS will demonstrate the new Remote Expert feature for its MobileHMI™ app, integrated with RealWear’s HMT-1 device. Previously, users could visualize real-time information, pull up associated manuals/documentation, and review step-by-step instructions on the HMT-1. New this year, the field service technician will be able to call upon an “expert” for help in troubleshooting difficult issues. Once connected with the expert, he or she can share a live video stream, photos, or even the current display with the expert, who can then verbally guide the technician, even adding annotations to the shared images to help visually convey exactly what the technician needs to do.
Using ICONICS’ software solutions for fault detection/diagnostics, scheduling, and guaranteed notification of service technicians, as well as advanced UIs and “expert” capabilities within mobile, hands-free devices, can provide customers with an innovative, proactive, cost-effective Connected Field Service solution.
To learn more about these exciting innovations in field service operations, watch the solution video at
www.iconics.com/cfsvideo