IFS study: Servitization and Aftermarket Contracts Pay Off for Manufacturers
Companies offering annual aftermarket service contracts 24% more likely to report profitability than those doing reactive field service work, as study conducted by IFS shows.
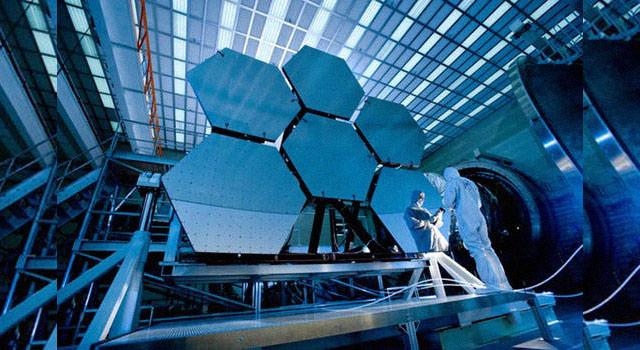
IFS, the global enterprise applications company, has released a research study of 200 executives to determine how industrial companies are progressing towards servitization—the expansion of manufacturing and product-focused companies into value-added service after the sale.
Servitization is of critical interest to industrial companies right now because growth of new product sales may be slowing, which means expanding into services is an appealing way to increase top line revenues. New technologies, including the internet of things (IoT), is enabling new service business models such as streamlined field service triggered by condition monitoring on products and equipment.
Analysts have been focusing on the desirability of servitization. McKinsey has found that the average margin for aftermarket services was 25 percent—substantialy more than the 10 percent realized on new equipment sales. According to a recent analysis by Frost & Sullivan, the North American market for calibration and repair services alone is set to reach almost $4 billion by 2022.
This study from IFS captures a snapshot of where industrial companies are currently on their servitization journey—whether they are selling products only, selling aftermarket parts, offering reactive field service, selling annual service contracts or offering asset-as-a-service or product-as-a-service—charging not for the product but for usage or productivity.
The study reveals that:
•Servitization maturity is tied to profitability of the service organization. Manufacturers involved in planned maintenance or service contracts were most likely to report service as a profit center with 62 percent reporting profitable service operations.
•38 percent of respondents sold only products, with no aftermarket or other service revenues.
•19 percent sold products and some aftermarket service parts.
•15 percent sold products and aftermarket field service through break-fix repair.
•16 percent sold planned maintenance contracts with service level agreements (SLAs).
•Only 4 percent of respondents reported full servitization—selling products on a subscription rather than a discrete item through power-by-the-hour, fee-for-usage or revenue sharing agreements. Companies operating in this fully-servitized business model include:
- 22 percent of medical device manufacturers
- 5 percent of metal fabrication businesses
- 5 percent of companies in the oil and gas industry
The study also explores how well enterprise software used by respondents prepares them for the digital transformation servitization requires, including whether they have integrated IoT data into their business systems to facilitate service.
- The fully servitized model, where a manufacturer may deliver a piece of equipment as a service, charging based on usage or through revenue sharing with their customer, requires a high degree of technological sophistication, IFS Senior Evangelist, North America, Tom DeVroy said.
- But even companies selling annual maintenance contracts or break-fix repair can benefit from integrating IoT data streams with their field service management software to improve responsiveness, automate the dispatch of technicians based on conditions of the product or just to gain an understanding of how their customer is using their products so they can sell to them more effectively.