Hazards in the Food Processing Industry
Journalist and activist Upton Sinclair revealed the horrors of the food processing and manufacturing industry when he wrote “The Jungle” in 1906. Sinclair’s groundbreaking book offered a behind-the-scenes look at life in Chicago’s turn-of-the-century meatpacking plants, and his unflinching reporting led to industry-wide reform and improved safety efforts throughout the United States.
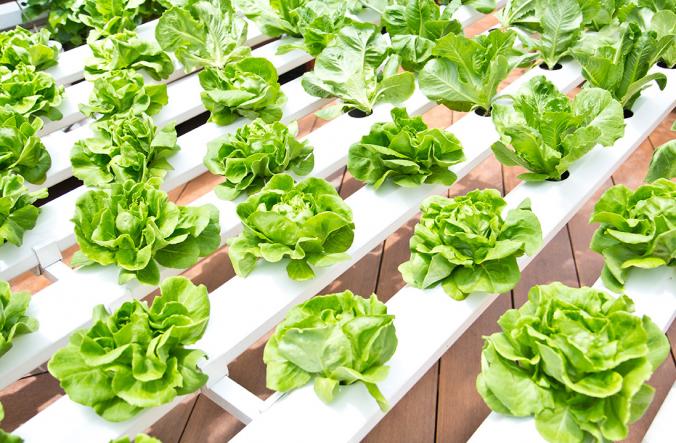
Yet even with technological advances and new regulations, workers in the food processing and manufacturing industry continue to face numerous health risks more than a century later. More than 19,000 food-manufacturing employees were injured on the job in 2015, and nearly 50 industry workers were killed each year between 2011 and 2015.
What are some of the common hazards workers encounter, and how can employers keep them safe on the job? Here’s a look at safety in the food processing and manufacturing industry.
Machinery Hazards
Machines used to clean, process, and package food are wrought with risks and hazards. Each year, more than 700 U.S. workers are killed in machine-related accidents, and another 2,500 are injured.
These workers face a number of hazards, including conveyors with moving or exposed parts, collapsing structures, falling objects, and compressed equipment.
For all the dangers that come with high-tech machinery, a few risks are more common than most. Those include:
- Machine guarding: Employers must provide guards to protect workers from moving and/or exposed parts.
- Lockout/Tagout (LO/TO): Machines and electrical equipment must be properly shut down, de-energized, and locked out during maintenance and servicing; when proper precautions aren’t taken, workers face increased risk of burns and electrocution.
- Loud noises: They might seem like a minor inconvenience, but loud noises may prevent communication between employees, increasing the risk of injury.
LO/TO violations are routinely among OSHA’s most-common citations every year. Protect your workers and comply with federal regulations: Download Graphic Products’ free Best Practice Guide to Lockout/Tagout for detailed directions for establishing a LO/TO program, as required by OSHA.
Safer food industry machinery
Conveyors are common in the food processing and manufacturing industries, and visual communication can protect workers from hot surfaces, exposed and moving parts, pressurized systems, and more.
The Conveyor Equipment Manufacturers Association (CEMA) has developed standardized safety labels to keep workers safe around conveyors; these designs comply with standards established by ANSI and use three signal words to communicate the seriousness of a hazard:
- Danger signs and labels communicate the most serious hazards, where death or serious injury is likely to occur if special precautions are not taken.
- Warning signs and labels outline hazards that can result in death or serious injury—but only when the overall risk is not severe enough to warrant a “Danger” sign.
- Caution signs describe hazards that may lead to minor or moderate injuries if not avoided.
Threats from Release of Ammonia
Workers sustained 1,280 injuries from exposure to harmful substances or environments in 2015, and many of those involved the toxic chemical anhydrous ammonia.
Throughout the United States, anhydrous ammonia is a popular refrigerant in food processing and manufacturing facilities. The substance can be found in breweries, juice and soft drink processing facilities, meat processing plants, and other food processing plants.
Despite that ubiquity, ammonia poses numerous risks to workers. Those hazards include:
- Corrosive: Ammonia can cause damage to the skin, eyes, and lungs.
- Flammable: Ammonia can be lethal at concentrations of roughly 15% to 28% by volume in air.
- Explosive: If released in enclosed spaces with a source of ignition present, ammonia can cause life-threatening explosions.
Protecting food workers from ammonia
For a safer environment, U.S.-based food processing and manufacturing plants must label all pipes that transport ammonia in accordance with International Institute for Ammonia Refrigeration (IIAR) Bulletin No. 114, the accepted standard for labelling ammonia refrigeration systems.
The standard requires employers to label system components, such as compressors, pumps, and receivers, and maintains that every ammonia pipe marker include the following five components:
- Piping Abbreviation
- Physical State
- Pipe Contents
- Pressure Level
- Flow Direction
Each component label must include a component identifier and indicate the pressure level, as well.
Slip, Trip, and Fall Dangers
Slip, trip, and fall hazards are among the most common causes of injury in both the food manufacturing industry and U.S. workplaces in general. In 2015 alone, more than 4,500 workers were injured in slips, trips, and falls, and 800 workers were killed in slip, trip, and fall accidents.
Given the high volume of liquids used in food manufacturing and processing, workers are regularly exposed to wet and unsafe surfaces. Workers can easily slip in puddles of water, trip over uneven surfaces, or fall when trying to access a platform.
OSHA’s standard for walking-working surfaces, 29 CFR 1910.22, requires the following for ensuring clean working areas:
Workroom floors must be clean and dry (whenever possible), and employers must mitigate hazards caused by inclement weather, loose boards, spills, and more.
Employers must provide drainage and dry standing places (such as floor mats) when wet processes are used in commercial food processing plants and other facilities.
All walking-working surfaces must be inspected and maintained in safe, working condition.
Reducing slips, trips, and falls in the processing plant
Floor marking and wayfinding tape is one of the easiest, most efficient solutions for mitigating slip, trip, and fall hazards.
Here is how floor tapes help workers stay upright, safe, and mobile:
- Tread Tape: Basic tread tape helps workers “grip” the surface, even when wet, preventing slips and falls.
- Tread Plates: When working on uneven or loose surfaces, bolted-down tread plates help improve traction in a variety of conditions—and on a variety of surfaces.
- Tread Caution Steps: Yellow-and-black textured plates keep workers safe on steps, entryways, ledges, and more.
Text: Matt Wastradowski, Graphic Products
Related reading: 8 Ways to Identify and Eliminate Noise Hazards in the Workplace