Asset performance 4.0: new technologies bring new solutions
Maintenance is teamwork - always and everywhere – and because of this, Bemas no longer considered it opportune to honour a single maintenance manager. That is why the emphasis this year was on ‘projects’.
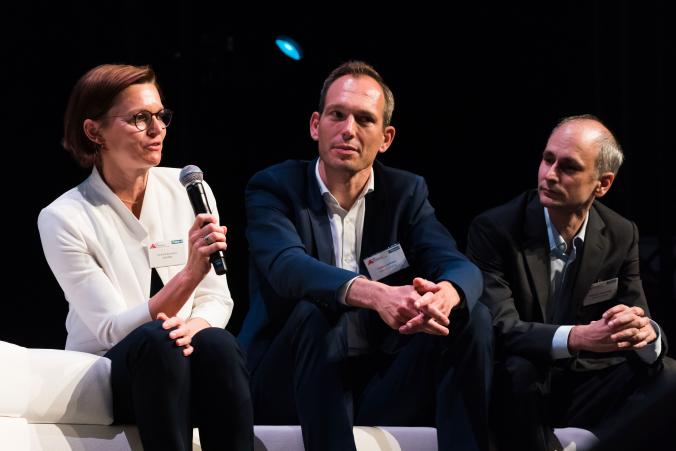
The brand new ‘Asset Performance Awards’ were awarded to interesting maintenance initiatives in three categories. It is no surprise that ‘4.0’ was an important topic. After all, the global evolution towards digitisation, Industry 4.0 and new technologies open the doors to solutions that the maintenance world has never thought possible. – ArcelorMittal took home the Asset Performance 4.0 Award.
We embraced technological evolution from the outset, says Andy Roegis, manager of industrial digitalization. The potential for production as well as quality, maintenance and logistics became clear fairly quickly.
Certainly, for our division, numerous new possibilities are opening that allow us to carry out maintenance in a more focused and efficient way, maintenance engineer Pieter Van den Branden continues.
The achilles heel of production
At ArcelorMittal, the digital transformation revolves around, among other things, increasing production reliability. The top priority was the hot strip mill in the Ghent plant, a machine that fulfils a crucial role.
It rolls slabs of steel of 23 cm to slabs of 1.5 mm thickness, which are then transported to the rewinding zone via a conveyor belt. There they are wound up into steel coils, says Pieter Van den Branden.
Unfortunately, the hot strip mill is the Achilles heel of the production. This sub-installation has 340 AC motors, each of which controls a transport roller. And that’s where things often go wrong: failures in the motor or the universal joint regularly cause an unforeseen machine standstill. This causes the entire production to come to a standstill. In addition, the plates are often scratched and have passed over a defective transport roller. In short, there is both a downtime and a quality cost!
Bringing together data sources
A logical answer to this problem was predictive maintenance. Yet for years it proved impossible to put this idea into practice.
Ordinary periodic vibration measurements did not provide enough data to define specific maintenance actions. In the end, we resorted to current and voltage measurements. In addition, we opened up the digitisation register further with the intelligent (self-learning) SAM4 software from SemioticLabs. This solution detects anomalies and generates warnings, even weeks before the breakdown will occur. And our efforts are paying off, because in the meantime the availability of the roller has increased considerably, said Andy Roegis.
It is important to note that all monitoring systems are integrated, Pieter Van den Branden continues.
The data from the ERP system are used to optimise the planning of the maintenance teams. Conversely, the SAM4 software returns all data from monitoring and maintenance to the ERP system. This is not so much about big data, but rather about bringing together different data sources. In order to gain additional knowledge to plan maintenance even better, he adds
Unseen opportunities
For Infrabel, the manager of the Belgian railway infrastructure who also competed for the Award, Industry 4.0 is a strategic necessity.
Although we are very active on the labour market, we have been faced with a shrinking workforce for several years now, project manager Sandrine Rauwoens states.
The influx of technically trained people is too small to cope with the outflow of pensionable employees. The message is therefore to work more efficiently. And digitisation is one of the ways to achieve this. In addition, we naturally want to keep up with the changes in society. New technologies, such as artificial intelligence and IOT, will determine the future. This also applies to the railways, and therefore also to Infrabel, which is responsible for the maintenance, renewal and expansion of the infrastructure. However, we are happy to go down this road. In the field of maintenance in particular, unprecedented opportunities are opening up. Measuring is knowing. Digitisation and new technologies allow for better planning and more efficient execution.
Faster and safer
A good example of this can be found in the ‘Prodigis’ project. In short, it concerns an optimisation process to secure the tracks for maintenance work.
This is a complex and highly regulated process, Sandrine Rauwoens explains.
Several procedures must be followed, each with different parties. The procedures vary according to the location and the work to be carried out. Until ‘Prodigis’, everything was done with paper forms and telephone communication, so that securing the tracks could take up to several hours. Prodigis’ is a textbook example of digitisation. We replaced a 100 percent paper-driven process with a 100 percent digital process in which process optimisation and user-friendliness are the main idea. Because the administrative part has been completely removed, we save a lot of time and the error rate is zero. This also benefits the safety of railway employees. Although ‘Prodigis’ is only a pilot, the end users are already very enthusiastic. They were also closely involved in the realisation of this digitisation project. Now a few extra procedures need to be added, after which we will roll out ‘Prodigis’ geographically throughout Belgium from next year.
Added value for clients
SPG Dry Cooling was also one of the competitors for the award. This engineering company is known for its Air-Cooled Condensers (ACCs), which are used worldwide in power stations with a power cycle.
As an innovative leader, it is our job to help customers optimize their systems, aftermarket manager Frederic Anthone says.
In doing so, we aim for maximum performance of the ACCs in particular. After all, optimal capacity utilisation has a tremendously positive impact on the electrical output and the overall performance of the assets. However, ACCs do not always perform in the same way because they react quite strongly to the specific circumstances of the moment. Wind direction and speed, ambient temperature, cleanliness of the heat exchange surface, ... influence the operation. Throughout the total lifecycle many fluctuations occur, so many power plant users and operators have no idea what the maximum performance of the ACC’s actually is. In order to solve this problem, we needed a technique that could process gigantic amounts of information using advanced analytics tools. This made it possible to determine patterns and relationships in data, both in steady axis and in transient operation.
Increased operational reliability and efficiency
With the surge of IoT and machine learning, SPG Dry Cooling realised what seemed impossible before.
We built a dedicated IoT ecosystem that provides actionable insights to the power plant operators about the performance of the steam cycle, innovation and technology manager Christophe Deleplanque explains.
The ACC360 combines the thermo-physical modelling with advanced analytics. With the processed information, clients can now optimize the net electrical output and net plant heat rate. Above that they can forecast accurately the electrical output based on the actual asset condition. With this project we bridge the gap between operational performance and reliability, which allows us to provide the customer with a total asset management tool.
Thanks to the use of advanced analytics and machine learning, we can develop a specific digital twin for each installed asset. This is a virtual representation of a physical product or process, used to understand and predict the physical counterpart’s performance characteristics. With this solution, we offer our customers real added value: we guarantee a better operational reliability and an optimisation of the return on investment. This gives us an excellent example of how rapidly evolving technology formulates answers to challenges that previously seemed unsolvable, Frederic Anthone concludes.
The Asset Performance 4.0 Conference & Exhibition offers a unique opportunity to learn how new 4.0 technologies and fundamentals in operations, maintenance and asset management reinforce each other to achieve higher equipment reliability and cost performance.
Do you have a project that will inspire your colleagues? Or do you want to share first-hand experiences with disruptive technologies? Let us know your presentation idea on www.assetperformance.eu.