The Challenges of Monitoring Mobile Mining Equipment
The monitoring of mobile equipment brings substantial challenges that must be addressed to ensure accurate, repeatable, and reliable data acquisition.
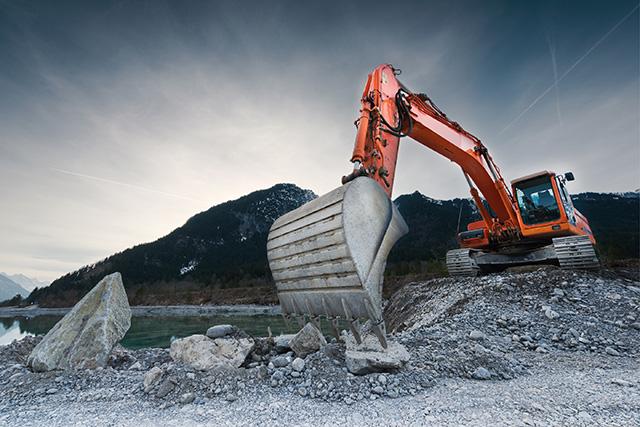
Vibration measurement has come of age in the last 20 years. While the practice of continuous online monitoring of critical machines in the oil, gas, and petrochemical industries has been commonplace for several decades, it is only recently that companies who had been using intermittent data collection techniques are now embracing continuous monitoring.
The benefits are substantial! The new horizon is mobile equipment draglines, shovels, bucket-wheel excavators, stacker-reclaimers, heavy haul trucks; all are equally important to production and just as critical as a gas compressor. However, unlike stationary machinery, monitoring mobile equipment brings substantial challenges that must be addressed to ensure accurate, repeatable, and reliable data acquisition. Rapid speed and load variations are just one element of the application.
The logistics of sensor mounting, cabling, network communications, and general serviceability, bring unique complications to the task of monitoring these machines. There are now new solutions available that have the potential to bring significant reliability improvements to large mobile equipment.
Speed and Load Variations
Reliable and repeatable vibration measurement has historically been dependant upon steady-state conditions, which are constant RPM and constant load. Repeatability, often regarded as the cornerstone of good vibration data collection, is essential for the accurate assessment of machine condition, and more so for intermittent monitoring strategies. The data must be representative of machinery health and reflect real changes due to incipient fault conditions and not to changes due to variations in operating conditions. As an example, when speed varies over the duration of a typical measurement cycle, adverse effects result:
• Affecting the reliability of the data and more importantly
• Compromising repeatability
One solution has been to perform the vibration measurement task on the machine in a quasi steady -state condition. Consider a typical mine shovel as illustrated on the next page.
During routine PM inspections the shovel is stationary at level ground and the 2000HP electric motors are run at constant speed under no-load. Vibration measurements at each of the motor bearings (NDE & DE) are reliable, repeatable and do not suffer from the variations due to operation of the bucket, crowd, swing, or crawl.
The limitation of testing in this manner is that fault conditions may only be evident while the equipment is under load, and so the data may be of limited use. Some would say it’s better than nothing! But perhaps there is a better way through selective triggering, based on RPM.
Defining a repeatable condition of operation or machine state which can be identified through the measurement of certain parameters, such as RPM, direction of rotation, and load, will help ensure that vibration data acquired during this machine state will be reliable and repeatable.
In Figure 2 the variation with time of both the RPM and the corresponding vibration level would pose serious problems for meaningful trend data. The establishment of a machine state based on measured parameters, in this case RPM and direction of rotation, will ensure a measure of repeatability and give confidence to trended vibration levels.
Order Tracking and Analysis
In some cases the machinery RPM varies continuously, without even a short interval when the speed is in a pseudo-constant range, making the establishment of a machine state difficult. Normal FFT analysis would result in smeared spectral components due to the fast changing RPM over the period of one FFT record length.
The smearing of the frequency components arises due to the fixed sampling rate of the FFT process, the rapid change in RPM, the fixed FFT record length, and the corresponding variation in level and frequency of the vibration.
Order tracking is a process whereby a specific frequency component as an example, the 1X, is extracted from a composite of frequency spectra versus RPM. The method is particularly useful for run-up or coast-down measurements where the speed changes occur over a short span, typically 1800RPM to 300RPM, and at a relatively moderate slew rate. The raw data when presented in an X, Y, Z, display is known as a waterfall plot, while the extracted components are referred to as slices (along the Z-axis).
The technique of order tracking is used most often as a diagnostic tool, as opposed to a continuous online monitoring method, and is principally employed to identify machinery resonances within the operating speed range. The extracted slices versus RPM (Z-axis) provide the analyst with a clear picture of how the amplitude of the individual frequency components such as the 1X may be exciting certain natural frequencies in the machine structure. Again, the measurement must be carefully configured to avoid smearing, taking into account the FFT record length (T*), RPM interval, and slew rate.
Order analysis on the other hand synchronizes the FFT sample rate with the machine RPM. In the past this procedure was performed in real-time using a tracking frequency multiplier whereby the sampling frequency was derived as an integer multiple (order) of the RPM.
In modern digital signal analysis, the time signal and RPM signal are recorded, and the order analysis is performed as a post-processing function whereby interpolation of the RPM signal yields a re-sampling rate applied to the time signal and the subsequent FFT creates the order spectrum.
State-of-the-art online continuous vibration monitoring systems using order analysis provide operators with a reliable and repeatable method of comparing order spectra versus time to visualize trends that arise due to machine condition and not RPM, see Figure 3.
Hardware Installation and Logistics
The selection of machines and corresponding measurement points follows criteria similar to the monitoring of stationary equipment. Those are typically criticality ranking, maintenance history, accessibility and safety considerations.
However, there are a few points peculiar to mobile mine equipment requiring additional scrutiny:
• Sensor connectivity and accessibility
• Equipment location within the mine site
• Network communication and PC software configuration
Sensors such as accelerometers are built to withstand harsh industrial conditions, but where cable runs in stationary installations are in a relatively static environment, mobile equipment sensor cables require additional protection against chafing. Small diameter hydraulic hose has been used successfully in these installations.
Drilling and tapping for transducer mounting may not be permitted particularly during warranty periods since many OEM’s are unfamiliar with the principal behind vibration monitoring and/or may simply object to the attachment of non-approved apparatus by third parties. Some major manufacturers do make provision for accelerometer mounting, but this is often an afterthought and is usually not the ideal measurement point.
Current monitoring systems employ TCP/IP network communications and can be equipped with a wireless modem for communication with the in-house Wi-Fi network. Some manufacturers of online vibration monitoring solutions offer hosting of the application and data via cloud servers. This option is becoming increasingly popular and offers many solutions to the questions of in-house network security or outside vendor access.
The networking element of the installation requires careful planning, disclosure, and a full understanding of ownership of the data. The IT department are the key players in the installation of the software, configuration of the network, and granting access to the vendor via the cloud, TeamViewer™, or remote desktop applications.
Lastly, mine equipment that is completely mobile such as heavy-haul trucks may be required to stop at a data waypoint due to Wi-Fi coverage to upload measurements to the network. Figure 4 provides a generalized view of a typical mine shovel monitoring application.
Mine managers, operators, planners, and maintenance personnel are not vibration analysts. They need timely, actionable information about equipment health via a quick and simplified user interface, without waiting days for VA reports.
Mobile mine equipment represents huge capital costs – it is expensive to operate, expensive to maintain, and critically important to mine productivity. Vibration monitoring has provided significant savings for many years in the maintenance and operation of stationary plant equipment.
Today, with advances in signal processing, transducer design, and networking options, mobile machinery operators can now begin to take advantage of the benefits derived from vibration monitoring – reduced downtime, lower operating and maintenance costs, decreased spare parts inventories, optimized PM schedule, improved equipment availability. The path to reliability-centred maintenance is becoming clearer. Remember – when you want something you have never had, you need to do something you have never done.
Originally published in MRO Magazine, 2015.