Stock It? Don’t Stock It?
I live in Kansas City, Kansas; the Westport District. If you are not from that area, you most likely are not familiar with the districts of KC. But, like most cities, Kansas City (Kansas and Missouri) are divided into areas or districts, ostensibly a by-product of the communities that came together to form the metropolis.
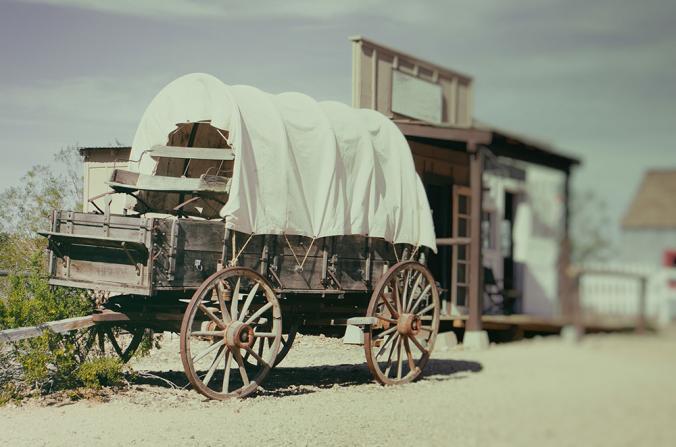
Westport is famous, at least it is for history buffs. This is the area where the Santa Fe and Oregon Trail wagon trains provisioned-up for their journeys west. One last stop in civilization to get those critical, often life-preserving supplies, before heading out into the great unknown.
Imagine those times, those hopeful events, and all the planning and preparation that went into a logistic execution that quite honestly, your life depended on. Things really have not changed that much in 150 years.
What do you take, what can you take, what is your limit? How do you preserve perishables while you are travelling? Are there other provision points along the way? What do I have or need that is repairable, how do I repair it, and what do I need in order to repair it? How about defensive equipment and supplies? Face it, you were limited by what your team of horses could pull. Each wagon, or grouping of wagons had to be a bit self-sufficient, but the enterprise, as a whole, had to be creative in sharing and resourcing amongst themselves to get everyone safely to their destination. You did not want to be a burden on the wagon train, but then again you could not take everything. Did you need it, or just want it?
Fast-forward 150 years and, in many ways, we are still having the same discussions. Wagon trains, and indeed the development of the West were successful in part because people learned and improved the process as they repeated the journey. For certain, the steam locomotive really opened the West for everyone, but before then it was as described above, a group of hopefuls heading west for a better tomorrow.
The discussion we need to have today is one that has been perplexing us since those days, and quite honestly for much longer in our history. How do we know what to take, or more for our discussion, how can we be sure what to stock or not stock. In some small way, each of us is a small collection of people trying to survive and thrive in our environment. Some operate in larger cities, with many resources. Others in smaller communities, where resources are light.
Focus on budget
In an attempt to answer this question, I hope to generate a frank discussion and some robust dialog by sharing what we consider to be an effective decision tree that will answer this stocking question. My colleagues and I have, over time, come to assemble what we feel to be a very effective tool to arrive at a measured and well-vetted decision. It is critical at this point that the reader understands that the decision to stock or not to stock an item should not be an emotional, or biased decision (or worse, made on a whim); it is one that should be measured, pragmatic, and apply a standard and repeatable logic. Imagine a team of four horses pulling the weight of your storeroom along the entirety of the Santa Fe Trail. You simply do not have the capacity.
Most storerooms we visit and work with today have exhausted the square footage of their available space and are now working at occupying all the cubic footage. This is the result of a detached and feckless approach to determining what to stock and what not to stock.
We should begin by agreeing on a few fundamental aspects of a storeroom. We do not expect a chorus of agreements, but foundationally, we should start from the same general position.
Before we determine if an item should be stocked or not, let us first discuss a storeroom budget. In this instance, we are only talking about repair parts for our production or facility assets (production equipment for manufacturing and assembly plants; facility component for service companies, hospitals, universities, etc.). It costs something to keep an operation going, what is that value relative to spare parts? Our model is based on 1% of Estimated Replacement Value, or 1% of ERV. If your facility had an ERV of $100MM, we would expect an MRO value limit of $1MM.
I feel it necessary to tie in the Santa Fe Trail story again and mention that the $1MM load is the maximum that our horses can pull over the terrain and the distance. That is our limit.
We should next agree that whatever parts we do intend to stock (or not stock), are only those parts or items that appear on an asset’s Bill of Material (BOM). We are not going to stock everything on a BOM, but will only stock an item that does appear on a BOM.
Where do BOMs come from and who is responsible for obtaining the BOM? Much has been written on this, but to be concise, the BOM is the responsibility of the project engineer; maintaining the integrity of the BOM is the role of the maintenance planner.
Again, with our wagon train; we are only going to take items that are in support of the wagon itself, the horses, tack and rigging, and the necessities for human survival (food, water, shelter, clothing, defensive weapons, and tools). We are only taking items on our trek westward that support our mission and are associated with the wagon, horses, and the people.
Reliability Centred Maintenance
And, our last point of fundamental understanding is to consider an aspect of Reliability Centred Maintenance in understanding the function of an asset, and of a component. This is an essential nuance in determining if an item should be stocked or not stocked. Does it have a function that is necessary? If we do not know, understand, or appreciate the function, how do we know if the asset or component is important enough to put on our wagon?
Just to recap, for the sake of this discussion on what to stock, or not stock we will:
- Limit our MRO inventory value to 1% of ERV
- Only consider items (for stock or non-stock) that appear on an asset’s BOM
- First understand the asset’s function and then the component’s function
Warning…disclaimer ahead. What we are presenting in the presented diagram is a decision tree, built over the years, and vetted by learned individuals, just like yourselves. This is not necessarily meant to be the absolute final word in what you should stock or not stock, and its general in nature to cover a wide swath of industries. Rather, the point that we hope to make, and the message we hope to drive home is that you too should have a decision tree to guide you. A tree that is rooted in the fundamental nutrients we established in the paragraphs above. Solid thought guidance should be our legacy.
Critical or not critical
A few pull-out conversations before you review the Stock, Don’t Stock Decision Tree. First, your organization must also have an unbiased method to determine if a part is critical or not critical. Some wrongly label items as critical to ‘ensure’ the item is stocked. There are many schools of thought on the meaning of a ‘critical spare part’, only one element is to provide insurance against the need for the part. For this particular discussion, it is only important that the reader have some calculus that helps to arrive at this determinant.
The decision tree is a standard workflow. Each organization will need to create their own definition for the blocks associated with this decision tree.
For example: Is lead-time for component acceptable? You will have to determine the availability of each item being considered. Information on lead-time usually resides in the Item Master Data for each component in the CMMS. It is very important that this information remain current and examined at least annually.
Another example: Is stocking the item fiscally sensible? For this block, determine what your MRO storeroom inventory level should be. It was suggested earlier, that a target should be 1% of ERV. Whatever the value, in this particular block, the question is, “do we have capacity on our wagon for this item?”
Finally, when it is determined that an item will not be stocked, one other consideration should be addressed. “Is this an item that should be established as an Order On Request (OOR) item?” Some items that do not meet the criteria to stock, might otherwise be set up as catalogued items. These are items whose information on the component is known, and the part has a part number, but the collective reasoning is that the item should not be physically stocked. Caution should be taken to ensure that only items that appear on an asset’s BOM are set up as OOR.
Our Stock It, Don’t Stock It Decision Tree follows. Let’s have this discussion.