Increased Efficiency of Maintenance Execution at Cargill’s European Starches, Sweeteners sites
Cargill Incorporated provides food, agriculture, financial, and industrial products and services to the world. The company carried out a maintenance improvement project at eight of its production locations in Europe with the main aim of improving the efficiency of the maintenance departments’ work. Results of the program are good: with improved work execution efficiency and lower maintenance costs among outcomes seen at the plants that took part in the program.
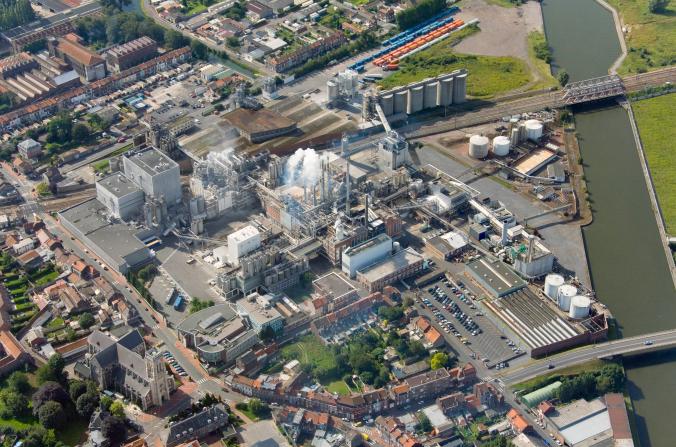
The company with a history of over 150 years of serving customers and communities in 70 countries has more than 150,000 employees worldwide. The Starches, Sweeteners & Texturizers division has several production sites in Europe. They produce gluten, glucoses and bioethanol, the main raw materials of which are wheat and maize.
Optimizing workforce utilization is a key priority for Cargill also at its European units. One of the key elements of the Da Vinci Maintenance & Reliability work management integration project at Cargill’s European sites was increasing work execution efficiency through an improved integration between maintenance and production.
According to Remco Jonker, Partner at Mainnovation, several factors contribute to lackluster wrench time. These include waiting for required spare parts and materials or unexpected travel. Planning and scheduling maintenance can help alleviate this issue. With the Da Vinci program, Mainnovation together with Cargill sought to find ways to boost wrench time at each specific site.
Cargill decided to go ahead with the Da Vinci to capture benefits on direct costs (maintenance) and indirect costs (i.e. more program duction due to reduced downtime). For this project we explored the market and we got in contact with Mainnovation for the first time, says Antonio Di Felice, Europe Maintenance & Reliability Manager, Cargill CSST.
The starting point of the maintenance improvement project was the process descriptions and best practices already available at Cargill, says Mainnovation’s Remco Jonker. The program began with a so-called Great Asset Management Experience (GAME) –kick-off –event.
At this stage all maintenance, production and plant managers came together to play this interactive maintenance management simulation in teams and to get ready for change. An assessment was then carried out at all sites in order to draw up a site-specific improvement programme, Jonker adds.
Both production and maintenance were involved in the Da Vinci program. The necessary changes were driven by the champions, each of whom took on part in the workflow at the sites. These champions were in turn supported by local Mainnovation change agents.
Jonker says that the project was characterised by a hard and a soft side. Performance management was used to provide insight in KPI’s and to identify the necessary improvements and to achieve them. In addition, softer elements were added from Mainnovation's Foucs+Change approach, such as the change readiness assessment, skill-will analysis and stakeholder analysis. Where necessary, people were coached in order to bring about the necessary behavioural change.
Main focus in Cargill’s project was sustainable change, Jonker adds.
Thanks to the in-depth practical maintenance expertise of the Mainnovation change agents, their experience with performance management and change management, and the maintenance experience and the desire to change present at Cargill sites, the locations managed to make the necessary improvement steps.
The integration with the production team in the daily coordination meetings was improved and works are executed more efficiently thanks to the improved work preparation process, Antonio Di Felice, from Cargill SST, says.
According to Di Felice, the feedback loop from the implementation has also led to considerable improvements. All in all, many losses in the execution have been removed and the overall efficiency has certainly been increased by 10-20 percent.
Moreover, work execution improved efficiency with consequent more efficient resources alignment to the sites needs in terms of maintenance works to be executed and additional production days thanks to an effective work planning & scheduling.
In average we can estimate an efficiency increase by 15 – 18 percent versus measured efficiency at the project start. Absolute numbers related to this efficiency improvement are confidential, however the increase percent provided will allow to reduce work backlog without increasing number of resources, having more time to train our people and efficiently balance internal and external resources.
There is also a positive effect on additional available production. However, Di Felice says that this is coming from a combination of some other projects with which Da Vinci is fully integrated providing the foundation to allow improved performance in terms of production stabilization.
Cargill understands that the workflow is an integrated part of Production and Maintenance and should not be considered as just a Maintenance activity.
Nina Garlo-Melkas