Choosing Maintenance Strategy
Not using Predictive Maintenance today is like having a black and white TV at home. If you are using Predictive Maintenance, then what are the real benefits compared to other maintenance strategies?
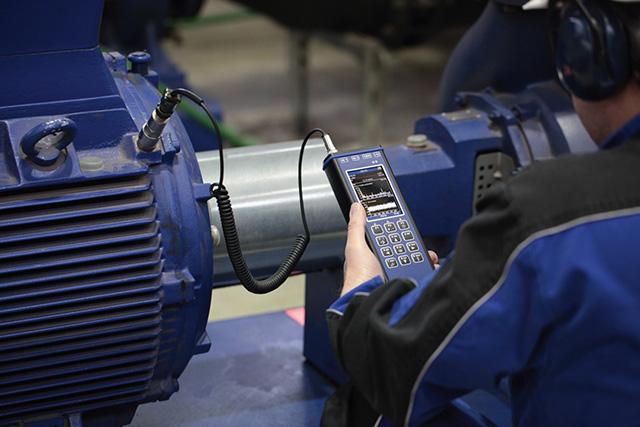
Before I joined the Adash company I had never heard about terms such as Predictive Maintenance, Condition Monitoring or Vibration Diagnostics. I was doing something completely different, but maybe destiny has wanted me to do this for more than 7 years now.
’What are those terms?’ I asked myself when they hired me. My target was to expand the Adash brand abroad but I was supposed to sell this ’product’ without any knowledge of it. Ok, a motor makes noises and you can also feel that it is shaking a bit while it is running.
I want to explain these terms simply to new maintenance people who have also never heard of them and who want or need to understand them. So you senior vibration analysts, please turn to the next page because this will be really boring for you!
Vibration in Rotating Machinery
Motors vibrate and the noise they make is in fact that vibration. I guess there is no need to explain that if you are speaking, your vocal cords are generating vibrations that are transmitted through the air to other people’s ear.
You cannot see these vibrations, but you can hear them. Imagine a bass speaker while playing some music. Can you see the movement of the speaker membrane? Yes, you can. But can you see the movement of the motor while it is running? Not really. There are some excellent tools available today that we can use to help us ’see’ a motor’s vibrations: the acceleration sensor and vibration meter or analyser.
If we go back to the speaker again, can you separate each noise that comes from the speaker while playing some music? Well, not each and every one of them, but if you have an equalizer, you can separate basses from trebles.
Why am I still talking about speakers? Music is very similar to the vibrations on the machine. On the machine you also want to separate those ’bass and treble’ noises but here we are talking about separating machine faults, such as overall machine condition related to shaft speed (low frequency) and bearing or gearbox faults (higher frequency).
For separating these faults we are using the above mentioned vibration meters and analysers. The overall machine condition and bearing condition are two basic things which we want to separate while performing Vibration Diagnostics. So, I hope this term is clear for you now.
Of course Vibration Diagnostics is more sophisticated and later on you will find out that you need to separate more vibration sources that are generated. For example from loose foundation bolts, unbalance, misalignment, fan blade faults, gear mesh faults and many more. But for now let’s just talk about those two basic things for an easier explanation.
There are more methods for evaluating a machine’s condition and its faults. Besides Vibration Diagnostics you may have heard about Ultrasonic detection, Thermography, Non-destructive Testing and so on, and all these methods are part of Condition Monitoring. That was simple, right?
The Importance of Maintenance Concept
Each method has its pros and cons; it will be up to your maintenance program which one you select and which one you use for your particular machines. But during the last few decades it has been found and proven that Vibration Diagnostics is the most efficient and reliable method for most rotating machinery.
Now my question is what kind of maintenance strategy is applied in your factory? I don’t believe that your company uses the oldest strategy, which is run-to-failure or so called ’breakdown maintenance’. If you have, for example, 100 people on a production line and the major machine that is critical for this production fails, you will probably send your staff home or give them another job, for example cleaning all the windows in the factory.
This would probably not be a big problem, but how much money will you lose while you are not producing for one hour? Or what if you have a dead line, your customer is waiting for your products and you are not able to deliver? You will loose this contract and possibly the customer as well because they will try to find a better supplier.
A better, but not ideal strategy is Preventive Maintenance or Scheduled Maintenance. This method is simple. For example every year you change the bearing on ’Machine Number 1’. The first aspect is financial; the bearing could be expensive and maybe it would run for more years if you knew its actual condition.
But ok, you install the new bearing and you expect that it will run for one year, because it is new. But what if the service company installed this new bearing badly? If it were badly placed it would produce excessive load on this bearing, would it still run for one year?
Take the Predictive Approach
Finally, we came to the modern method that belongs to the 21st century and its requirement of reliable machinery and continuous production. This is Predictive Maintenance. From the English term ’to predict something’ we’ve got a clue what this term means.
Predictive Maintenance gives you the biggest advantage against the two other methods above because it informs you about the actual condition of your machinery and you will be ready to take some steps with your machine prior to failure. But this method is not ’free of charge’, you will have to invest some money if you want to outsource it.
You can hire a service company to do this job for you. Of course there are a lot of companies that do this work well; they keep tracking your machinery every month or every two months and they always give you some feedback about your machinery.
But there are worse cases. I have asked one of my friends, who works as a maintenance guy for an alloy wheels company, if they do predictive maintenance. He said, ’Yes, there is some company which comes to us every half a year, they measure something and then they show me some graph of Spectra, but I don’t know what it means so I don’t care…’
Your company could pay a lot of money to these kinds of companies for nothing. A lot could happen in that half a year!
One thing is that your service company has no idea what kind of treatment you did with your machinery during that half a year. You could have changed or repaired something, but they don’t know about it and I don’t believe that they try to find out.
And if some machine fails you will complain to your service company, but they could tell you, ’Sorry, this is a sudden failure, probably a manufacturing defect’. And you can do nothing because they secured this ’sudden failure’ in their contract…
Or you can do it on your own, which will cost you some initial investment and also your time, but if you do it properly this investment will pay off very soon. The investment could be just half of the money that you are paying to an outsourcing company. You can start with a simple vibration meter or data collector.
Let’s assume that you begin to measure on a machine with perfect / optimal condition. Start with measuring and trending the above mentioned two values. So the first one is for overall machine condition and the second for bearing condition.
Measure them every month and keep checking the trend of values. Are these values still the same without any changes? If so, your machine is still ok. But once you see that any value is rising, you have got an indication that something is happening and you can plan a correction or repair in advance. Simple isn’t it? Don’t wait, start today!