Breathing New Life into Old Valves Boosts Productivity
Maintenance professionals pride themselves on preventing equipment from breaking down, or repairing it quickly. Replacing old equipment with new technology can be a good thing. But refurbishing a piece of equipment to like-new condition is often seen as equally good, sometimes even better.
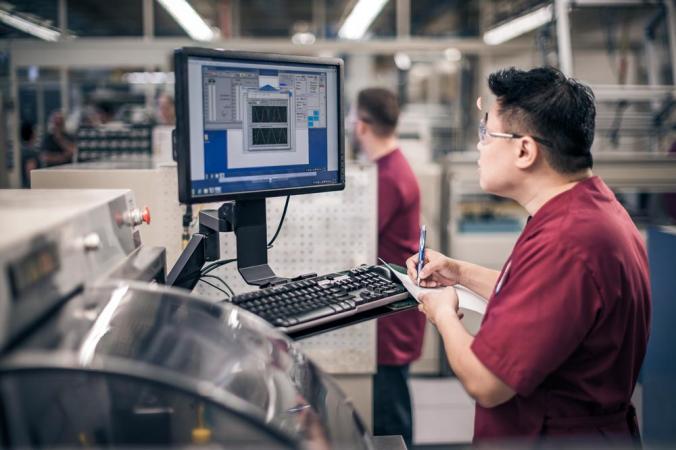
Moog – a maker of high-performance motion control technology such as servo valves for power generation, oil & gas production, steel mills, test systems and paper mills – recently launched the Return-To-Productivity Program to help maintenance managers in the Americas evaluate and refurbish their older, or even obsolete, valves. Since 2000, plant managers and equipment builders have put more than one million Moog Servo Valves into service.
The RTP Program gives maintenance professionals across a variety of industries the services to evaluate and repair the servo valves running their equipment. By launching the program, engineers at Moog hope plant managers will turn to Moog instead of an unauthorized repair house (URH). As part of the program, even if a maintenance manager has a Moog valve that turns out to be obsolete, Moog will clean the valve, evaluate its condition and provide users with an inspection report describing the health of the valve as well as recommendations for potentially replacing it.
Turning to an OEM to affect repairs or service equipment is a logical step. However, some maintenance managers do just the opposite because they believe asking the OEM to repair a piece of equipment will break their budget. The viewpoint of some maintenance professionals is that if they turn to an unauthorized repair house, or even bypass an expensive repair altogether, they will save money. Our experience is just the opposite.
For example, a steel mill had difficulty maintaining hydraulic system pressure on its gauge line. Its HPU system was robust with three 33-percent capacity pumps and a fourth pump in reserve. As the situation worsened, the mill was forced to operate the reserve pump, consume additional electricity and operate without a spare pump. At the same time, the pressures were declining and the fluid temperatures were increasing. The mill’s managers approached Moog and its local distributor for assistance. Moog audited the system and learned that the servo valves had not received a Moog factory repair in many years. Instead, a URH had repaired the valves.
Moog believed that the root cause of the steel mill’s problem was leakage through the servo valves caused by worn seals between the bushing and the spool. Moog maintains strict leakage standards for repairs and will replace the bushing spool assembly if the leakage is excessive. A URH cannot purchase replacement parts from Moog and will reuse worn parts as long as the valve is “functional.” The severe leakage explained the higher flow needed to maintain system pressure and the increased temperature as the hot oil was prematurely returned to the sump.
The mill returned four servo valves for repair. Moog determined that the internal leakage was eight times greater than it recommends. After inspection, technicians learned that some of the spools were not made by the Moog and were not manufactured to the correct tolerances. These were also an older style valve with a mechanical null adjustment. Moog’s team upgraded the valves to a more reliable magnetic null adjustment mechanism (at no additional charge). The valves were installed on the gauge line and the pressures returned to normal with only three pumps operating. Temperatures returned to normal too. This saved the company almost US$50,000 a year in electricity. And the valves have now been in service for more than two years without the mill having to return them to Moog for repair, which has yielded significant savings in maintenance costs.
Think Twice When Considering a URH
So while a URH might try to win business by asking a potential customer to compare the repair price per valve with that of an OEM, the maintenance cost added into a URH’s price ultimately makes it more economical to have the OEM service your servo valve. It is true that you can go to a URH and get what they would state is a “serviced valve.” We have seen time and again though, that these URH-repaired valves typically last between six and twelve months until a plant manager will see an unstable production platform caused by early fatigue in the valve.
Ultimately, that kind of “repair” causes poor product quality and higher scrap counts in production applications, or an unplanned outage in power generation and flight simulation. Any one of these things could lead to thousands (or hundreds of thousands) of dollars in lost product or productivity.
In contrast, when maintenance managers turn to an OEM to have their valves repaired, Moog, in particular, carries out these repairs by following ISO standards. Fastidiously adhering to industry standards, in turn, ensures that a plant or equipment operator can count on his or her repaired valve running for a billion cycles, which correlates to years of service.
The selection of high quality components is critical to minimizing unplanned downtime. The cost of operational loss during unplanned downtime whether it is industrial production or transportation justifies the time it takes an engineer to evaluate the life expectancy of critical components on equipment. For example, test stands and flight simulators are valued in the millions of dollars and the unexpected failure of a servo valve or actuator translates into lost revenues and schedule delays that can often exceed the original equipment costs. Early fatigue in the internal servo valve components generally do not exhibit any external signs of degradation such as leakage. However, the early fatigue definitely affects the dynamic performance of the servo valve. Once the servo valve is mounted in the equipment, most equipment operators will not be able to visually see any performance changes unless the system fails catastrophically.
For plant managers who still opt for an unauthorized repair house to solve their problems, they might be surprised to learn that sometimes the equipment in question still ends up in the OEM’s hands. We have seen instances in which a URH couldn’t repair a Moog servo valve, and they sent it to us in pieces. We serviced the valve and returned it to the URH. If the plant or mill operator had come directly to Moog or used a Moog authorized distributor, then we would have saved them time and money.
In fact, when time is critical, we have actually repaired a Moog servo valve and returned it by plane to its owner on the same day we received it. And while speed is sometimes of great importance, the quality of a repair is even more significant. URHs also lack the documentation to test a repaired part against the original specifications, which is a hallmark of quality repair. As part of Moog’s RTP Program, if a maintenance manager sends us a valve for repair and we note that our engineering team has upgraded that particular model of servo valve, we will upgrade the valve sent to us for repair as part of our standard services. Practically speaking that might mean our repair group would receive an older valve with a steel ball on the feedback wire, matched with a slotted spool. We would take it upon ourselves to upgrade the valve to incorporate a carbide ball on the feedback wire matched with the ball-in-hole spool design. Enhancements like this increase the longevity of the valve.
Calling All Valves
If a plant manager has valves in their equipment that are very old or obsolete, the RTP program is still an option. Moog’s repair technicians and engineers will evaluate these older makes and models of valves to assess the performance against the original specifications. Some of the assembly and test technicians who conduct this work for Moog’s customers have been in their roles for up to 30 years, so they have seen everything. Once they analyze a valve, the technicians and engineers can recommend if the valve can operate safely and, if not, recommend an equivalent Moog valve with aggressive trade-in pricing that meets or exceeds any competitor’s specifications.
For plants and factories that might have a large base of installed valves spanning many makes and models, Moog’s engineers can identify the proper replacements and develop a plan to minimize the number of valve models in operation at a facility. We like to refer to this analysis and planning as a way to reduce “valve sprawl.” By reducing various makes and models of valves inside a plant and relying instead on a common model for spares, maintenance managers can reduce their inventory rate.
Truly repairing your valves requires inspecting the hardware and providing an inspection (or repair) report that identifies what is wrong with the valve and how the valve is functioning. With our experience analyzing and repairing valves, we can also solve a plant manager’s problems on a system level, not just the component level. This is something else a URH is not qualified to do. If, for example, we see valves come back to us with worn spools caused by repeated contamination or a cracked flexure sleeve, our technicians can identify what is wrong with the system and recommend a system-wide solution.
And that is a guaranteed way of getting the most from your valves and boosting productivity.