Asset Care and Reliability in the Mining Industry using Ultrasound
Ultrasound applications are diverse and yet many people “know” about it for one or two applications. “I knew it did air leaks, but I did not know that you could do all this with it” is therefore a common reaction when I refer to eight pillars introducing the use of Ultrasound.
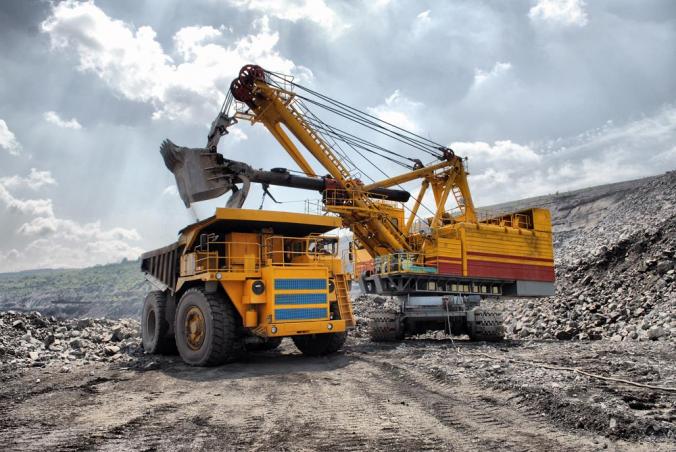
There are many industries where all of these applications are important and Mining is an example to explore.
1
Compressed air is used in so many applications. Compressed air leaks become huge energy losses – in some mines there are megawatts of power used to produce compressed air. Air leaks in pneumatics and control systems however, can become showstoppers, bringing production to a stop. Using Ultrasound for listening to internal air leaks or cracks on the boom of a dragline
2
Steam is of major importance in certain mining processes – consider the steam injection systems used in a SAG-D (Steam Assisted Gravity Drainage) plant for instance. Steam is injected underground to warm up and soften bitumen and heavier oils to make them easier to extract from the earth. The production of steam is thereby clearly linked to the production of oil in this application.
Airborne ultrasound is used to safely identify steam leaks from a distance, which is clearly a major safety hazard in any steam process. The steam temperature may be almost 300°C corresponding to a pressure of roughly 8,000kPa, which means leaks can easily become serious injuries or worse still, fatal accidents. There are sites around the world where the only safe, approved, method to inspect for steam leaks is ultrasound.
Contact ultrasound is used to maintain the good operating condition of the steam traps in the system by identifying those failing steam traps that are not removing air, CO2 and condensate from the steam system.
3
Valves are used in so many applications and are virtually omni-present in the mining industry – consider how a hydraulic or water system is going to operate properly without the proper operation of the valves involved.
Process failures tracked back to incorrect valve operation can create a large amount of unwanted downtime – one particular story in a coal mine comes to mind where an internal leak on a valve and also on the refurbished spare in the maintenance stores resulted in 12 hours of downtime. Ultrasound is now used to provide a predictive maintenance service to identify such defects at a much earlier stage and schedule work on the valve at a convenient time.
Everyone will understand the need to test valves to ensure that they are not passing or blocked, but there are other important failure modes on valves: valves will cavitate for example, which will result not only in premature failure of the valve, but can also cause premature failure downstream – especially if the particular valve is for example on the suction side of a pump.
4
Hydraulic systems are used for motion and for power and there are many valve applications involved here too. Failure of hydraulic systems is not an option and yet too few businesses consider any maintenance practice other than breakdown with the corresponding huge expense of downtime. Ultrasound can be used on shovels for example to listen to internal bypassing on boom, stick and bucket cylinders.
The inspection method for cylinders is quite simple: merely place a sensor on the cylinder and allow it to operate in its normal fashion
5
There are many electrical systems involved in the mining industry from DC to HV. In many cases dust is a major contributor to failure. One of the key problems associated with the build-up of dirt, dust and moisture on the surface of components is Tracking.
The ceramic insulator pictured in Figure 1. failed because it was covered in dust which was causing the tracking. On-condition cleaning using ultrasound to identify the presence of the tracking is used to eliminate failures by optimising cleaning procedures.
The mining community in South Africa is also leading the way in the adoption of ultrasound as a safety-screening tool to protect electricians working in substations. A small ultrasound kit is located at the entrance to the substation and there is a series of assessment measurements to be performed in order to provide approved safe access to the building and proximity to the panels inside. This approach is undoubtedly saving lives by providing a higher level of safety in the work environment than can be provided by flameproof or arc-flash clothing alone.
6
Tightness testing of the air intake systems of the large diesel engines in haul trucks using ultrasound has saved one mining company alone over $15M in three years for an investment of less than $30,000. Additional operational savings have been seen by minimising the time spent ensuring that the drivers’ cab environments are dust-free.
7
Mining machinery is diverse – sometimes simple like a conveyor, other times more complex as in the case of a reclaimer. The condition monitoring requirements in the mining world are therefore quite diverse and frequently not simple.
Airborne ultrasound, sometimes using a parabolic dish pointing out of the window of a pickup is a very quick and reliable means of inspecting the condition of a conveyor – especially if it is 12km long.
There is more than the usual amount of slow-speed equipment in mining, which is often in critical operational roles. Ultrasound is perfectly capable of listening to bearings rotating at even less than 1rpm and still providing valuable diagnostic information.
Finally, there is the need to consider the condition of machinery that is itself moving – like shovels, or that are moving violently – like vibrating screens.
A critical bearing rotating at 24rpm shown in Figure 2. was found to have failed during an ultrasound inspection. The bearing had recently been replaced, so it was relatively new. Unfortunately, the replacement bearing was not quite the correct one and was undersized for the load requirement. Very quickly, the new bearing disintegrated.
8
Over-lubrication is quite an established tradition in the mining world – “grease that bearing until I can see the grease coming out of the sides”. In a previous article in this magazine, I reported how one mine successfully reduced its lubrication consumption by over 95% whilst improving reliability against all established measures in place.w
So there you have it. One technology, Ultrasound, used in either airborne or contact mode to identify problems in 8 major problem areas in mining. Conservatively, in the last decade the savings that customers have achieved must be well beyond $25M. Time for you to start?