An Asset’s Potential for Reliability
If you design a piece of equipment poorly, build it cheaply, and install it hastily, you are not going to have a world class asset on your hands.
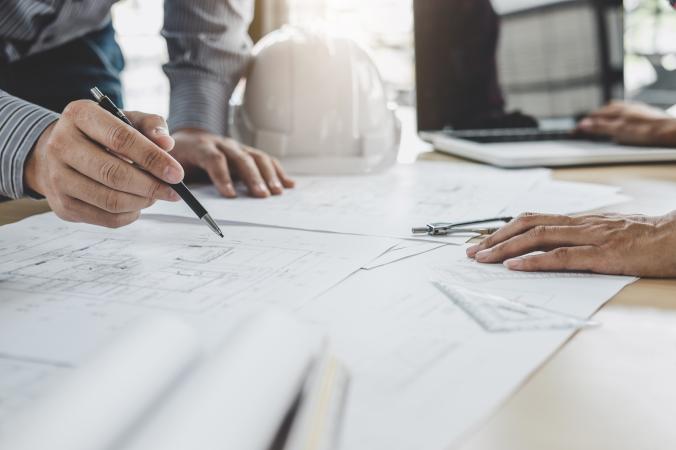
More likely, you are going to have a nightmare for the next forty years. Let us show that algebraically: D x B x I
This article is an enhanced excerpt from the newly released The Reliability Excellence Workbook, From Ideas to Action by John L. Ross, Jr.
We need to show this algebraically to indicate that an improvement in any of the three integers (D, B, or I) will improve the overall potential for reliability where the slightest miscue in any could cause a real and serious problem with the whole.
This formula is not calculating the inherent reliability of an asset, but what it does do is calculate our chance of having high reliability. Let us further our discussion by equating this, somewhat loosely, with calculating a system using block diagrams.
Using the formula
For an example, let us assume the following values:
For D—design, we have got almost a perfect, flawless design. This is a rock
solid proposal. We will give it a 99 percent.
For B—build, we have got the best OEM for this product, this is a five star manufacturer. Just to game our system a bit, let us give that a 99 percent as well.
For I—install, we are using our trusty ol’ general contractor that has been working in this plant for years. The old man himself is coming out to supervise this install. Everything is perfect, 99 percent.
Using the block diagram approach for calculating reliability, we have:
(.99 x .99 x .99) x 100 = 97 percent
We have done our part to design, build, and install the best machine possible. Near perfect actually. Now it is up to operations and plant maintenance to keep the asset humming at this exceptional level.
But, wait a minute, things never go as planned. Even the best intentions have to yield to the project budget.
We likely set out to design the best machine that is possible, not initially considering the cost. After all, let us at least ask for what we want. Our design, if we are doing it correctly, would hope to utilize the parts we already have in our storeroom. These are parts, for whatever reason, seem to survive in our environment. Why wouldn’t we want to build those into our new asset? This is standardization.
Our initial design might call for top-shelf components. We would plan for redundancy and built in diagnostics. It’s likely that our design would even include 110-V convenience outlets. Ours would be a fine machine, or, as Jules Verne penned in Twenty Thousand Leagues under the Sea, “There, sir! [sic] that is the perfect of vessels!”
Now comes concession time. We have to carve and round out some features to fit into the budget. Even the capital spares idea goes out the window. Pretty soon, our D—design goes from a 99 percent to an 85 percent.
The B—build does not fare much better. We are forced to go to the lowest bidder, this alone knocks us down a few percentage points. As we discover during construction, the component we actually wanted, does not physically fit, so we have to get another model that is almost as good. Since we did not specify the exact components we would accept, we end up with the components the OEM gets the best deal on. 99 percent becomes 82 percent, just like that.
I—install is the end of this adventure. We are utilizing space cleared from another machine, and we do our best to clean up the site. Someone has the cost saving idea to reuse the old disconnect and power distribution panel, saving at least $1,000 against our budget.
Earlier we had the bright idea to prepare the site with a vibration isolation pad, but we ran out of money. And, the cooling tower is a little under-sized, but it is bound to work. We had two weeks to install this unit, but the plant manager decided to run six days into that. Now we have eight days (one of those is Thanksgiving).
For all our trouble, I—install falls from 99 percent to 87 percent. I refer to these values as the EDE rating or Equipment Design Excellence rating.
Our calculation now stands at: .85 x .82 x .87 = 60.6 percent (a 60 percent drop). Where did it all go wrong?
I want to deviate slightly from this conversation to touch on the idea of running at a high OEE (Overall Equipment Effectiveness). Some consider 85 percent to be the world-class number, but I have also heard many arguments against there even being a high-level metric. Regardless, I’d like to point out that it might be near impossible to hit a consistently high OEE value with a machine that nets a 60.6 percent potential for reliability the minute you start it up in your plant. The greater point is the machine was never designed, built, and installed to hit an attractive OEE. Throw all the money you want or can at it, and it will be the nightmare we know it is.
Much of this can be improved, and indeed guarded against any decrease, by having set processes and procedures for capital projects and major repair projects and sticking to those processes. Also, we can give ourselves a better chance of success by having set component standards that we insist on. This helps not only the equipment design excellence effort, but the storeroom and the maintenance group in delivering maintainability. This process, as noted earlier, is defined as parts standardization and is one of thirty-two world-class storeroom processes. Like most of the storeroom processes, however, a great deal of success is predicated on the adherence and discipline of the maintenance and engineering departments. Have you ever had an engineer design the ‘wrong’ part on a machine? That was meant to be rhetorical.
There is a significant difference in what it will cost and how many joules of human energy will be needed to maintain an asset that comes at us with a 97 percent EDE rating versus a 60.6 percent EDE; it is 60 percent!
A note on where the numbers come from. How do you determine if the design is an 85 percent or a 90 percent? This is a fairly open scoring system, but one that does need to have some rules around it. In fact, as part of the capital and major repair process development, I would suggest that the group engaged in developing the processes further develop an unambiguous scoring system that can be used on all projects. The scale will not change. It is carved in stone. This is a system that is particular to you, your organization, and your company.
Let us run a very quick exercise to demonstrate the power of this number.
Give this exercise a try.
Write down the last capital project or major modification conducted in your facility:
On a scale from 0 percent to 100 percent, give a value to each of the three following categories:
Design:
Build:
Install:
Overall D x B x I =
Chances are, if the DBI number is <60 percent the asset has been hard to maintain and troublesome. If the number is >80 percent, it has been operating fairly well, and not much of a burden. A number that is in-between 60 percent and 80 percent is common territory and honestly the value we are likely to calculate for the equipment in our facilities. These ‘in-between’ assets will run fairly well by our better operators. Lesser skilled operators, or those with poor attitudes will seem to have more issues with these machines.
If you were conducting a post project review, of the project you just evaluated, what suggestions would you make to arrive at a higher D x B x I value?