Six Signs of a Successful Acoustic Lubrication Programme
Acoustic Lubrication is just one of the 8 application pillars adopted by world-class ultrasound programmes. And what an important one it is.
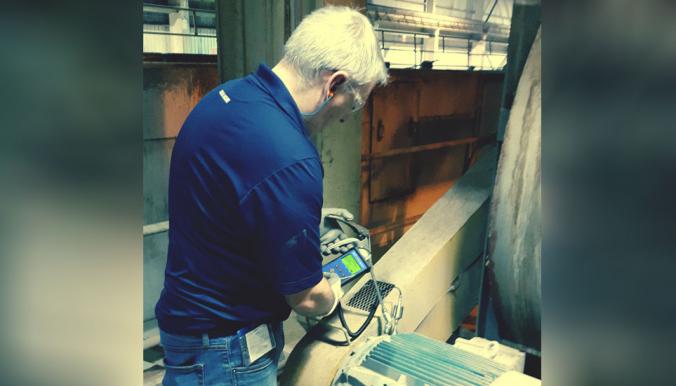
Poor lubrication practices account for as much as 40% of all premature bearing failures. When ultrasound is utilized to assess lubrication needs and schedule grease replenishment intervals that number drops below 10%. What would 30% fewer bearing-related failures mean for your organization?
Keep up with the changes in on-condition bearing lubrication or risk falling behind. For example, technology advancements from ultrasonic innovator SDT are transforming the way we look at the grease replenishment task. SDT’s LUBExpert, an ultrasound solution that helps grease bearings correctly, simplifies a complex process into a simple, 2-step procedure.
A successfully implemented world class, acoustic lubrication programme delivers many wins for your company. Reduced maintenance costs as well as other savings on grease consumption and less unplanned downtime are two big doors that open other possibilities for factory maintenance teams. Another win will be factory-wide efficiency. Properly maintained and lubricated bearings run more efficiently, using less energy and lowering their environmental impact.
With so much innovation available, the question begs, is your lubrication programme world-class? Here are six signs to help you decide.
Six Signs your lubrication programme is on track
1. A change in the quantity of grease consumed
Maintenance departments should track grease consumption to monitor and control costs. Root Cause Analysis on failed bearings points to over-greasing as the leading contributor. Bad procedures lead to bearings routinely receiving more grease than they are designed to handle. The excess ends up being pushed into the motor casing or purged onto the floor. Reduction in grease consumption is a sure sign that your lubrication programme is on the right track.
Over lubrication happens when grease replenishment intervals are scheduled based on time instead of condition. Control lubrication tasks with ultrasound to monitor condition and maintain optimal friction. The time between greasing intervals increases, resulting in less grease used per bearing.
Over-greased machines are not only more susceptible to fail, but run less efficiently. Optimally greased bearings draw far less energy and contribute to a greener factory. That alone should be motivation enough to Grease Bearings Right.
2. Fewer lube-related failures
Your organization should track failures and perform root cause analysis to eliminate sources of defects.
Optimized greasing programmes experience fewer lube-related failures. Less fixing and fire-fighting translates to more creative time for maintenance. Use that time to bring more machines into the greasing programme.
Additionally, with ultrasound you find many non-trendable defects. For example, broken or blocked grease pipes and incorrectly fitted grease paths that prevent grease from reaching the bearing.
3. Optimized MRO spares management
Your new and improved lubrication programme is delivering wins; better control of grease consumption, fewer failures, and more productivity for maintenance. Use this time to study trends and better manage your storeroom.
A decrease in bearing-related failures improves spares optimization. Share your ultrasonic lubrication data with your MRO Stores manager to create a plan to reduce the number of emergency parts on hand.
Since you are taking stock, why not shift some burden to your suppliers? Ask them to confirm your emergency parts against their own stock. If it can be supplied on the same day then why keep it on your balance sheet?
4. Increased number of machines monitored
One benefit of an effective lubrication programme is time.
- Time allotted to monitoring machines instead of fixing them.
- Time allotted to correctly assessing the real needs for lubrication.
- Time to look at the big picture.
Take for instance, criticality assessment. Many lubrication programmes begin with small steps. All the “A” critical machines receive priority, rightly so. But what about the rest? With more time to plan, organize, and schedule, increase the number of machines acoustically monitored for optimal lubrication.
5. Save time. Combine acoustic lubrication and condition monitoring
You worked hard for these results. It is time to use your data for more than just lubrication.
Acoustic lubrication is the proven method to ensure precise bearing lubrication. New technology from SDT, LUBExpert, combines the power of onboard lubrication guidance with Four Condition Indicators for bearing condition assessment.
The time savings from assessing bearing condition during the lubrication process is beyond valuable and another sign your acoustic lubrication programme is on the right track.
6. Inspector Confidence at an All-Time High
Reliable machines are the product of an effective lubrication programme. You have:
- Managed grease consumption
- Fewer grease-related bearing failures
- Optimized MRO spares
- More machines under watch
- Increased data collection intervals
The power of adding ultrasound to your greasing programme delivers win after win for reliability. Reliability breeds confidence. More confident inspectors make better decisions and infect a positive culture throughout the organization.
Ultrasound-assisted lubrication of plant assets offers significant benefits that calendar based lubrication cannot. Lubrication serves a primary purpose, which is to create a thin layer of lubricant between rolling and sliding elements that reduces friction. So, it makes sense that the best way to determine the lubrication requirement of a machine is to monitor friction levels, not time in service.
Machines that are properly lubricated require less energy to run. Imagine that reducing grease consumption can lower your energy bills. Machines that consume less electricity run cooler and enjoy longer life cycles.
Finally, by monitoring the condition of your machinery’s lubrication, you are at the same time collecting valuable condition data about the machine itself. Dynamic and static ultrasound data coupled with the 4 condition indicators (RMS, Max RMS, Peak, and Crest Factor) are all indicators of bearing health.
Optimizing lubrication of plant machinery with ultrasound results in a significant reduction in grease consumption. Successful ultrasound programmes accelerate the velocity of positive culture change.
Who knew so much good news could come from such a simple shift from calendar to condition-based maintenance?
A Heat Pump Plant Turns the Carbon Footprint of Textile Fibre Production Negative
Valmet launches intelligent fiber furnish control to secure better refiner operation
Valmet introduces the Valmet Fiber Furnish Control application package for board and papermakers to stabilize refiner operation for maximized production efficiency with ensured furnish quality. Based on real-time measurements of multiple fiber properties and freeness, the control features advanced feedback and feedforward solutions together with model predictive control.