Improve Industrial Processes
When creating smooth and efficient systems for the process industry, energy absorption and vibration reduction are two important elements plant managers must consider.
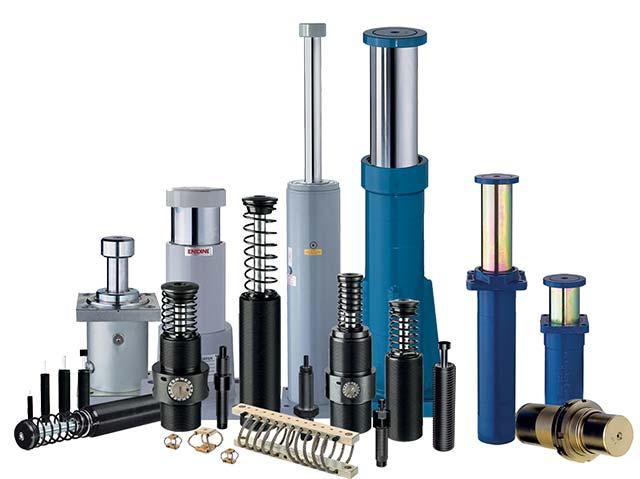
The installation of custom-engineered energy absorption products throughout your facility can reduce cost, increase efficiency and machine reliability, ensure product quality and consistency and even keep employees safer.
Any precision motion task creates a lot of kinetic energy that needs to be managed. Throughout the manufacturing process, there are many abrupt stops, starts, turns and vibrations that can adversely affect an object during its travel time, making the entire operation more susceptible to costly failures and unexpected downtime. To keep important processes online, with less downtime and equipment failure, plant managers should look to energy absorption products, which can manage this kinetic energy and reduce vibration.
Take for example a chemical manufacturing plant. The chemicals must flow from an inception point to the packaging facility without damage to the product or the equipment. Throughout its flow process, this chemical may experience stops, starts and turns, which create energy and vibration.
Without energy absorption products, this energy and vibration is transmitted to the product and your equipment. Shock absorbers and vibration reduction equipment are necessary to ensure successful chemical flow and protection of your machine’s components.
Controlling Energy to Decrease Damage and Downtime
There are many areas of a manufacturing process where energy absorption should be considered, but managing the kinetic energy behind the start/stop process is crucial to maintaining an efficient operation. A manufacturing process without engineered energy absorption has limits to the speed of operation.
If the process isn’t properly controlled, and your equipment is operating above or below these limits, you could be damaging your product and equipment or losing efficiency. Finding a balance between these extremes is imperative.
To cushion the start and stop impact, shock absorbers are used at all points where motion change is expected. However, there are many variables that must be considered when choosing the right shock absorber, such as product weight.
If you are using shock absorbers, but they are not the correct type or are tuned incorrectly, it could cause further damage and downtime. An industry partner can work with your facility to engineer shock absorbers that are the proper size and are tuned correctly, resulting in the lowest transmission of impacting force to equipment.
Case Study 1. The start/stop process is a critical element within the coal manufacturing process. This process involves a series of equipment, including a coke oven Larry Car, coke oven Quench Car and coke oven pusher machine.
The function of the Larry Car is to charge the coke ovens with coal. The pusher machine ultimately pushes the coke cake from the oven, through the coke guide and into the quench car.
Once the coke cake is inside the quench car, the car travels down the track to the quenching station where the coke is quenched by water. After quenching, the car is taken to a coke wharf where the coke is discharged.
In all three cases, if the braking machine fails or the operator over-travels the car or machine, the equipment must be stopped safely, overcoming both the momentum and, in some cases, the driving force of the motor as well. The stop must be gentle enough to prevent damage to the machine, cars and other equipment, or injury to the operator.
In the case of the pusher machine, another problem can arise: stopping the pusher ram. There are control systems that limit switches to stop the ram. If these systems fail, the ram must be stopped, overcoming both the momentum of the ram and in some cases the driving force of the motor as well.
ITT Enidine’s Jarret shock absorbers are ideal for these applications because they provide full energy absorbing capability at the low operating speeds common with this type of equipment. Since the reaction of a Jarret shock absorber increases with stroke, they will not bottom out when the machine or car is driven into them.
As they are stroked, the reaction increases to overbalance the drive force of the equipment with enough remaining capacity to remove the kinetic energy, thereby assuring a gradual, shock-free stop, without reaching the end of the stroke.
Jarret shock absorbers are normally selected to provide emergency stop capability with low deceleration forces in power on impacts to avoid injury to operators. The Jarret units can be mounted on the cars or pusher machine to impact against the end structure or they can be mounted on the end stop structure that the cars or machine impacts.
Controlling Vibration and Preventing Machine Fatigue
As opposed to the abrupt movements that generally signify a need for shock absorbers, uncontrolled vibration causes long-term wear-and-tear, general fatigue and degradation of assembly components, such as loose bolts and broken welds.
If your facility uses automated optical imaging to ensure product consistency or check for errors in the manufacturing process, vibration can affect image quality and impair the camera’s ability to view the product effectively.
Vibration control devices can be used to manage the vibration and extend the life of assembly components. Control applications, such as wire rope isolators, isolate the vibrating assembly pieces, protecting the surrounding equipment. Isolating the surrounding equipment prevents loosening bolts, breaking welds, and damage to essential electronic components. This prevents costly maintenance, reduces downtime and improves productivity.
Case Study 2. A central California manufacturer of produce and food handling equipment was in the process of designing a produce dryer, part of a complete production line that begins with removing produce from a truck and finishes with bag-sealed produce ready for purchase by the consumer.
However, the manufacturer was concerned that uneven, wet loads would emit vibrations that would transmit into the mounting frame assembly. Vibration can cause damage to internal components, electrical devices as well as other nearby equipment.
ITT Enidine Inc. application engineers worked together to create a solution to isolate the vibration, incorporating ITT Enidine Inc.’s Wire Rope Isolators into the units. Stainless steel bars were added to the isolators, helping to eliminate potential wash-down problems. To prevent produce bits from lodging into the cable strands, the wire rope units were sealed with moulded rubber.
During production tests, the dryer units ran with 1500 lbs. of wet produce turning at a rate of 600 RPM and very little vibration was registered in the frame assembly. The custom engineered, moulded High Energy Rope Mount (HERM) units effectively solved the vibration problem.
If your facility is experiencing equipment wear and tear or frequent down-time, motion control solutions to control vibration and energy should be considered. Motion control technology can be custom-engineered and tuned to your facility’s unique needs, which will keep your important processes online, increase efficiency and product quality and decrease downtime and costly equipment failure.
A Heat Pump Plant Turns the Carbon Footprint of Textile Fibre Production Negative
Valmet launches intelligent fiber furnish control to secure better refiner operation
Valmet introduces the Valmet Fiber Furnish Control application package for board and papermakers to stabilize refiner operation for maximized production efficiency with ensured furnish quality. Based on real-time measurements of multiple fiber properties and freeness, the control features advanced feedback and feedforward solutions together with model predictive control.