Choosing the Best Tunnel Boring Machine for Mountainous Conditions
Geology in high cover tunnels is often complex and Tunnel Boring Machines (TBMs) have proven themselves in deep tunnels worldwide as a fast, safe, and cost-effective solution that can be customized to project conditions. This article will explore the advantages of mechanical excavation, what types of TBMs are best suited for certain ground, and important considerations for ground support in high cover conditions.
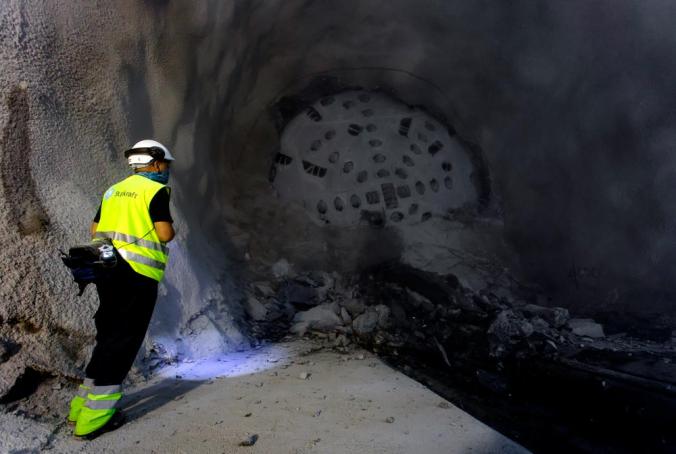
In mountainous tunnels under high rock cover, the true ground conditions can be difficult to predict, even with information collected from an exploratory tunnel. Factors like squeezing, fault zones, caverns, and water can all be missed with a full-sized tunnel and a meter-by-meter analysis of ground conditions is often impractical if not impossible. When one considers the excavation method required for such varied unknown conditions, many factors need to be evaluated such as versatility and investigational methods like continuous probe drilling and pre-grouting.
Main Beam TBMs
In even the most extreme ground conditions, Main Beam TBMs (also known as “open-type” machines) can be efficient and safe. Features such as open access behind the cutterhead for ground support and consolidation, unrestricted probe drilling, and the absence of a shield are all-important attributes in extreme conditions. In ground exhibiting squeezing-convergence and rock bursting, open-type machines often fare better than shielded machines, as they are less likely to get stuck. They can also utilize the McNally Support System, in which the curved finger shield plates are replaced for a curved assembly of pockets with rectangular cross-sections. In swelling-slacking ground Main Beam TBMs also allow for immediate ground treatment behind or over the top of the cutterhead. Open-type machines are capable of operating in ground with occasional to continuous water as long as a mitigation strategy combining grouting to stem flows, as well as pumps to remove the water, is employed.
Shielded Hard Rock TBMs
Most shielded TBMs line the tunnel either simultaneously with or directly after a TBM stroke, resulting in an earlier useable date for the tunnel. Shielded machines also have the very beneficial advantage of providing a limited section of non-heavy support; i.e., the distance from the cutterhead to the grouted lining. Shielded TBMs can also have difficulty in faulted rock, as the working area for ground consolidation can somewhat restrict good face coverage. There are two types of shielded hard rock TBMs: Single Shield and Double Shield.
Single Shield TBMs are shorter in length and can therefore be launched from a shorter starter tunnel, and are typically utilized in non-self-supporting rock, as the machine advances by reacting against the concrete tunnel lining rather than unstable tunnel walls. They have the disadvantage of not having grippers, which allow greater pull, thrust and jogging of the cutterhead.
Double Shield TBMs are ideal in self-supporting rock, and some non-self-supporting rock, or in combination ground since they can react against either tunnel walls or segments. The shield also provides protection from rock falls and other problems, making it ideal in hard, blocky ground as well. In addition, in squeezing ground Double Shield TBMs can be used with compressible material as backfill or special segments to accommodate squeezing conditions.
Both types of machines can be successfully utilized in a wide range of conditions—even in squeezing ground and significant water inflows—if properly designed. A host of technology, termed Difficult Ground Solutions (DGS), can be used on these machines, from multi-speed gearboxes that enable excavation in fault zones to shield lubrication and breakout thrust/torque for squeezing and collapsing ground.
Advancements in ground support
Squeezing/Convergent Ground
For squeezing or converging ground, over-boring is often necessary. The only practical solution to over boring is to pre-mount extra gage housing in the periphery of the cutterhead. In the over-bore zone, yielding type structures should be erected if using an open-type machine. These structures can include yielding steel arches, steel arches in conjunction with yielding jacks, shotcrete structures with yielding rock anchors, or combinations of the above supports. Such support needs to be placed with assistance of the ring beam erector or some other mechanical means. The most desirable location to place such support is immediately behind the cutterhead—a problematic situation with a shield type machine. The machines also must be equipped with very high torque to overcome the squeezing effect.
If using a shielded machine erecting segments, certain features such as a convergence measuring system—a hydraulic cylinder mounted on top of the machine and connected to the machines computer system (PLC)—can detect when squeezing conditions are present. Having a machine designed with the shortest possible shield length, and a stepped (tapered) shield if necessary can be immensely helpful. As mentioned previously, shield lubrication and emergency thrust can get a machine through a situation where it might otherwise become trapped.
Rock Bursting
In rock bursting conditions wire mesh with rock bolts, yielding rock anchors, steel arches, ring beams or combinations of all the above may be required. Such support can be placed with rock drills, a ring beam erector, and a shotcrete system. It is important to hold the rock in place to control and limit the disturbance of the rock to as great an extent as possible. Rock bursting could also be contained with TBMs in association with special lining.
With modern open-type TBMs, ground support such as the McNally Roof Support System can be used to allow lining to be extruded from the machine as it advances—a very safe option in these conditions. Today’s TBMs are also equipped with all of the same tools and techniques that are used in drill & blast operations to excavate through difficult rock conditions. With sophisticated probing techniques installed on the TBM, the operator can predict what is ahead of the tunnelling operation more quickly than drill & blast and react appropriately. On a shielded machine, probe drilling is equally important. The machine’s shield provides safety against rock bursting events.
Swelling/Slacking Ground
In swelling and slacking conditions an effective ground treatment is shotcrete applied immediately behind the cutterhead, for both open-type and shielded machines. In extreme conditions, over-boring may be required and measures for rock support in squeezing ground may be needed. The support can be a combination of shotcrete, rock drills and ring beams on an open-type machine. The difficult question, however, is to predict the extent of swelling and squeezing. This is a very important consideration when considering the use of concrete segments in such conditions. Because of the difficulty of predicting the extent of swelling, two-pass lining systems have been used such as in the large diameter Niagara Tunnel Project in sedimentary rock. This large diameter (14.4 m) tunnel utilized initial ground support followed by a slipform concrete liner and a waterproof membrane.
Fault Zones & Water Pressure
Fault zones can be the most difficult condition to encounter, especially when associated with water under pressure. They are also the most difficult conditions for predicting expected advance rates.
In all conditions, advance probe drilling is recommended 30 to 40 meters in advance of the face with a 10 m overlay. This is especially important when fault zones or water are expected. When a fault zone or water is encountered, the extent of the zone should be explored prior to TBM boring within 10 – 20 meters of the zone. Drilling should be done on a 360-degree basis. First, the zone should be grouted to stop water inflows. After grouting, ground consolidation additives should be injected into the unstable rock or soil material. It may be necessary to inject such material into the face at short intervals of 2 to 4 meters, and advance at shorter intervals. The support of geologists experienced in predicting and treating fault zones, and of ground conditioning experts, is highly recommended when fault zones are encountered.
For passing through fault zones, grout and ground conditioning holes are required. After ground treatment, ground support such as spiling or forepoling through the front shield over the cutterhead may be necessary for safe and predictable advance. It is preferable to carry on this drilling as close to the face as possible to ensure good face coverage. These methods are all possible whether an open-type or shielded machine is used.
When water is present in a hard rock tunnel, it can be pumped away from the face and out of the tunnel (even fairly significant water inflows). However, if there is a possibility of significant pressures and/or a massive inrush of water, then a shielded machine with DGS features is recommended. In the event of a large inrush of water, a guillotine gate on the muck chute can effectively seal off the muck chamber to keep the crew safe as well as keep the machine from becoming flooded out. Additional inflatable seals can seal the gap between the telescopic shield and outer shields of a Double Shield TBM to keep everything watertight. This system is termed “passive” water protection because the TBM is stopped in place (not actively operating). During that time the crew can then work to grout off water inflows and dewater the chamber to control the flow before they begin boring again.
Blocky or Jointed Rock
In blocky or highly jointed rock, the McNally system to hold the rock in place has been proven very effective in open-type machines. If the rocks are held in place then this can prevent or lessen the condition of cathedralling over the cutterhead and fallout in front of the face; it will also reduce cutterhead damage. The ground support should be placed as close as possible to the cutterhead. Rock supports for the McNally system can be prefabricated rebar, wood/metal slats, or wire mesh in conjunction with rock straps and rock bolts. In a shielded machine, DGS features previously mentioned including shield lubrication, tapered shields, and hydraulic shield breakout—where radial ports in the machine shield can be made to inject pressurized hydraulic lubricants to free a shield that has already become stuck—are all useful.
A Heat Pump Plant Turns the Carbon Footprint of Textile Fibre Production Negative
Valmet launches intelligent fiber furnish control to secure better refiner operation
Valmet introduces the Valmet Fiber Furnish Control application package for board and papermakers to stabilize refiner operation for maximized production efficiency with ensured furnish quality. Based on real-time measurements of multiple fiber properties and freeness, the control features advanced feedback and feedforward solutions together with model predictive control.